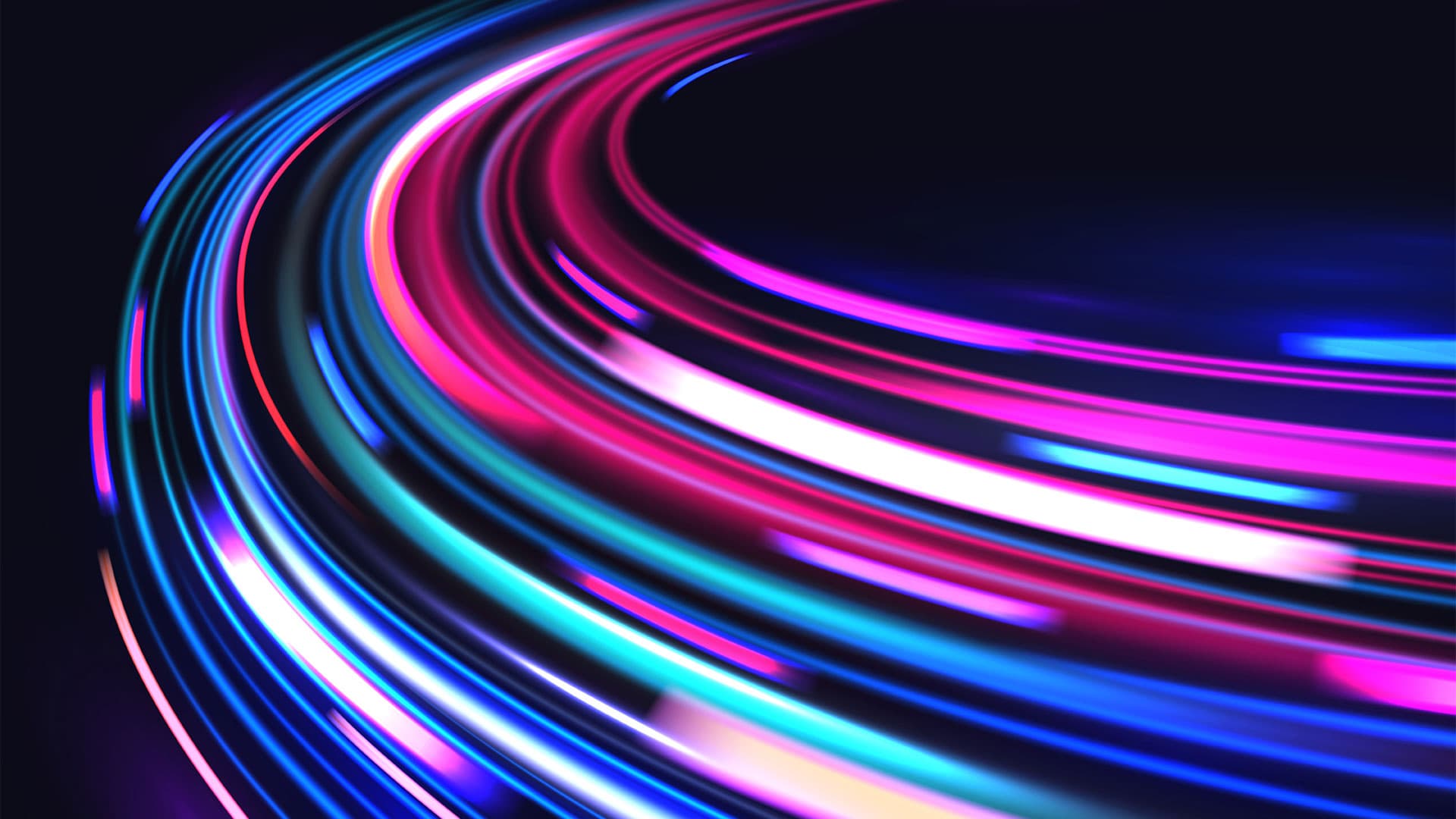
EP3 - From ideas to impact - Building tomorrow's proptech
Explore how proptech is reshaping commercial real estate with tools that deliver real ROI, streamline operations, and enable a more connected future.
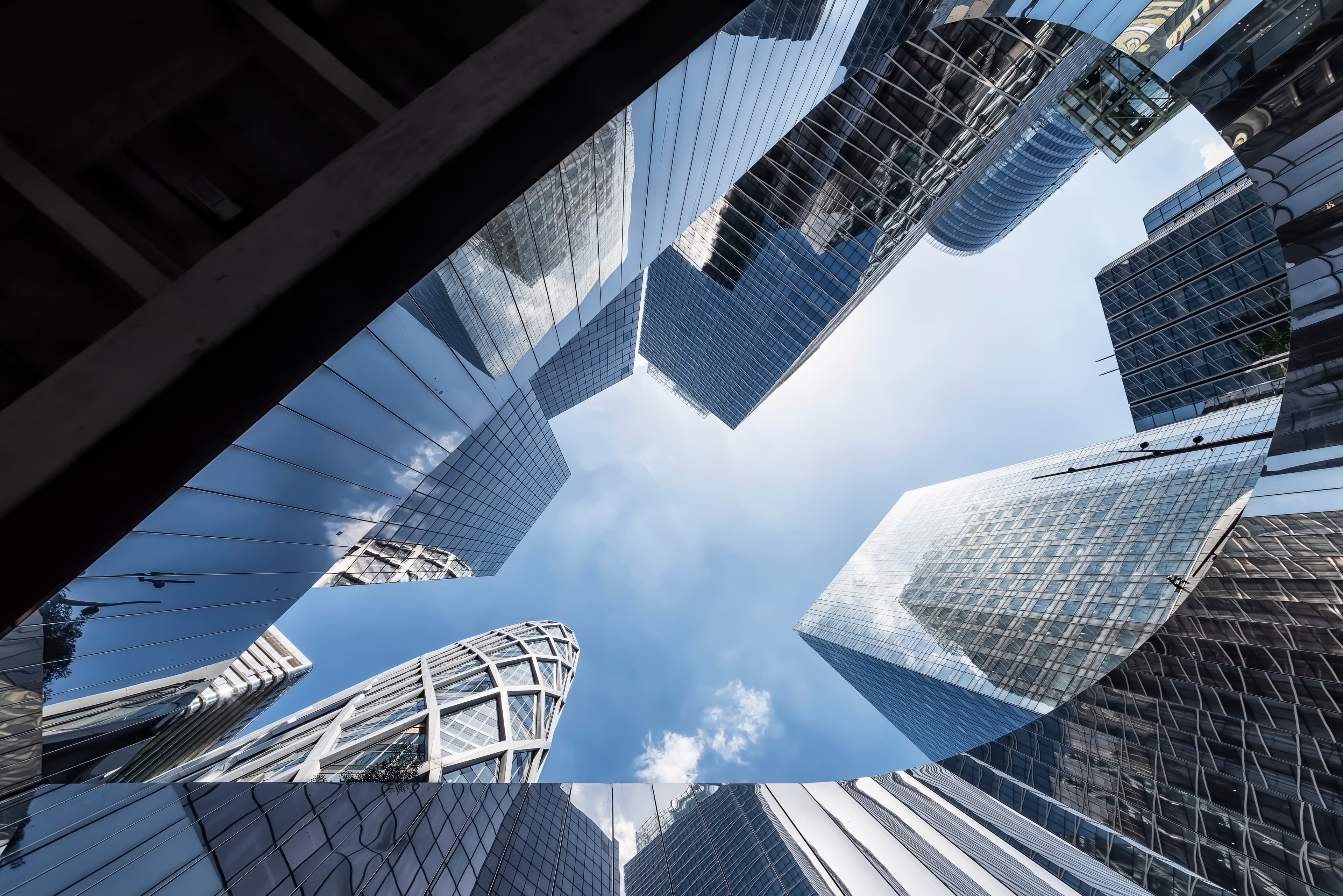
Scaling smart in European CRE with valuation management outsourcing
As European CRE markets rebound, learn how outsourcing valuation management helps funds scale quickly, stay compliant, and refocus internal teams on high-value priorities.
What a quarter century of transaction data tells us about US commercial real estate
We examine the long-term trends that have reshaped the commercial real estate landscape and what they may suggest about its future.
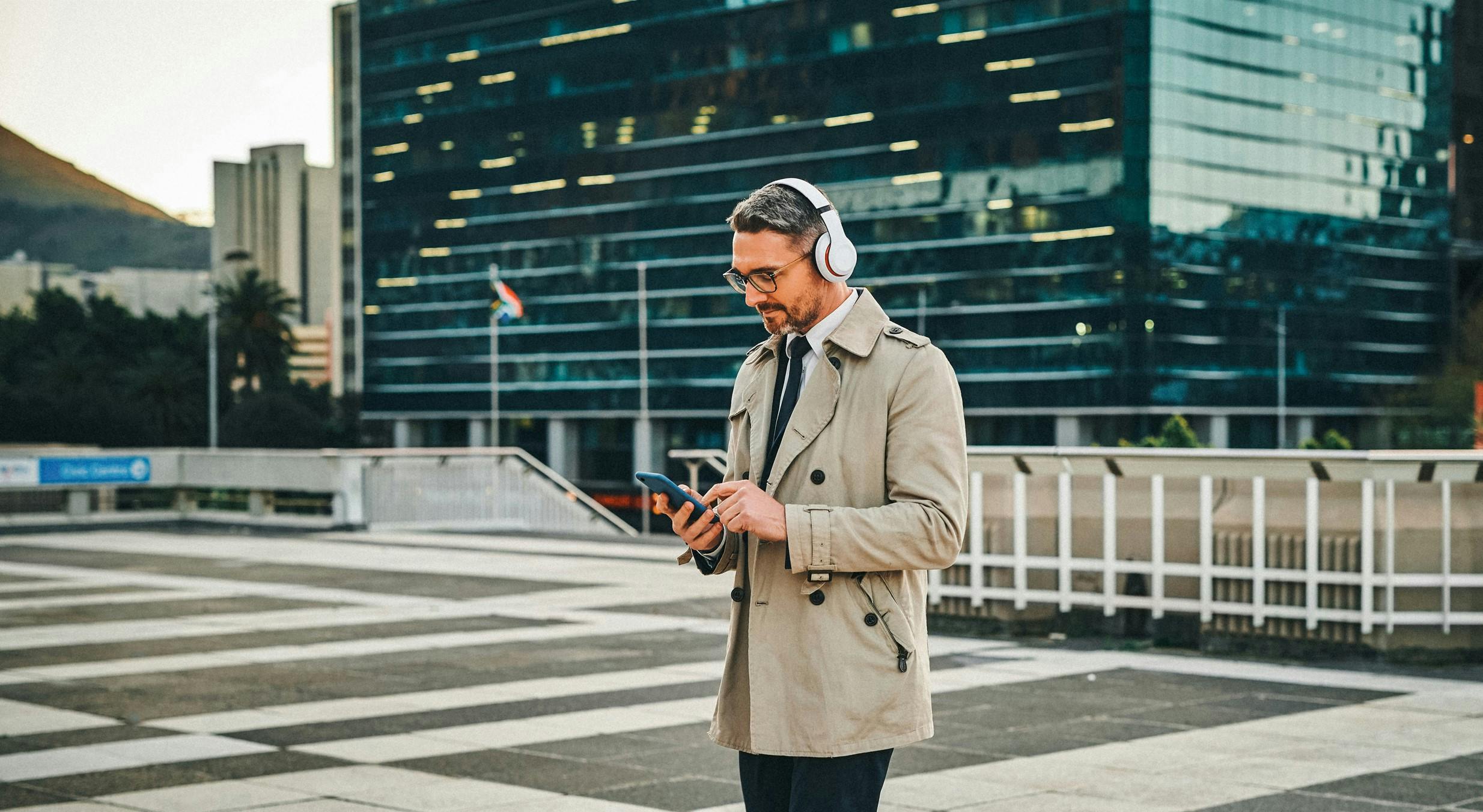
EP68 - Just how liquid is commercial real estate?
Dr. Philip English joins us to explore how liquidity shapes CRE investment decisions and why new research may challenge traditional market assumptions.
Featured
Insight
Research
Podcast
Resources
Latest insights
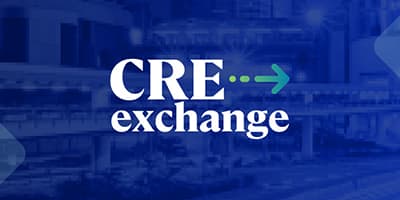
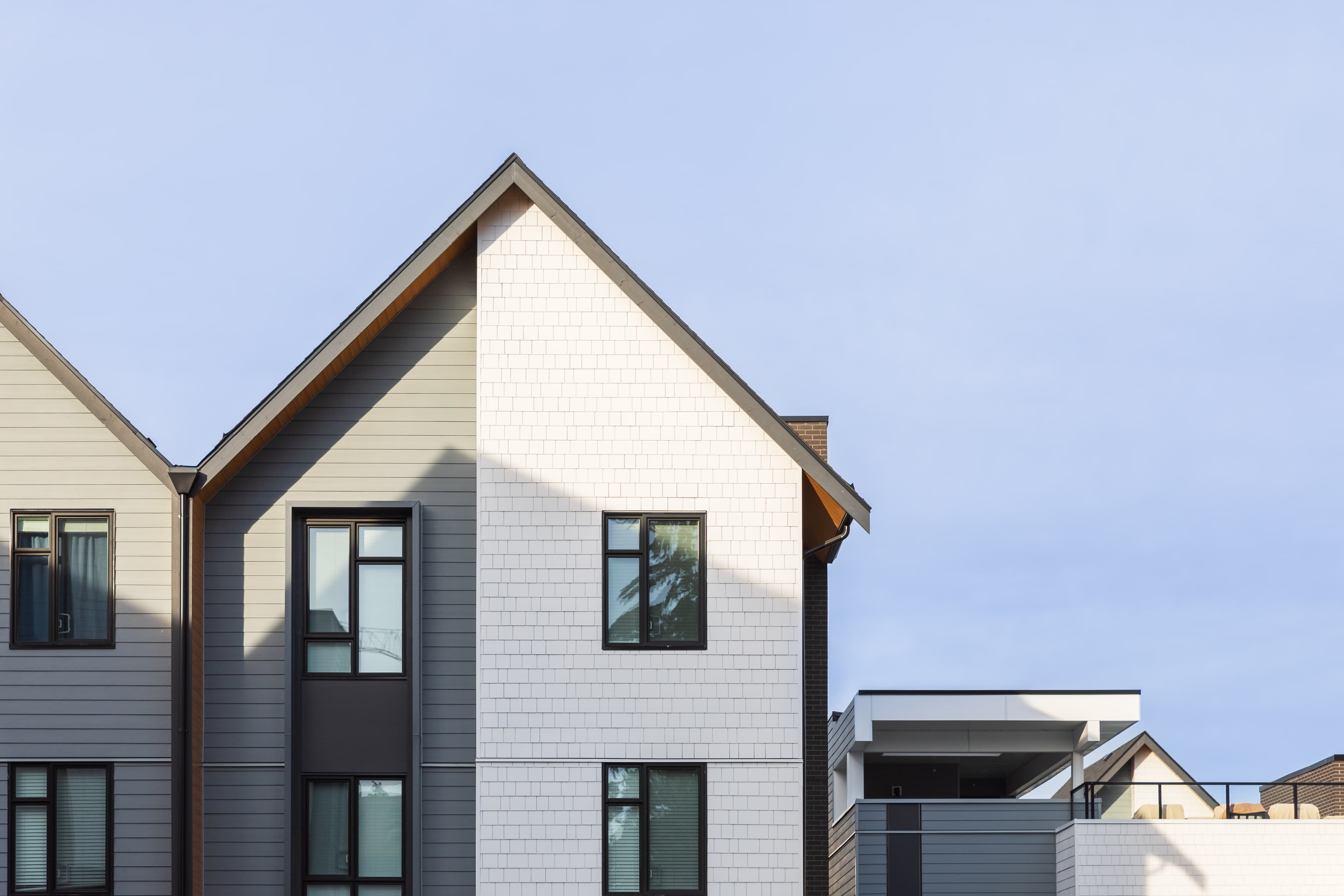
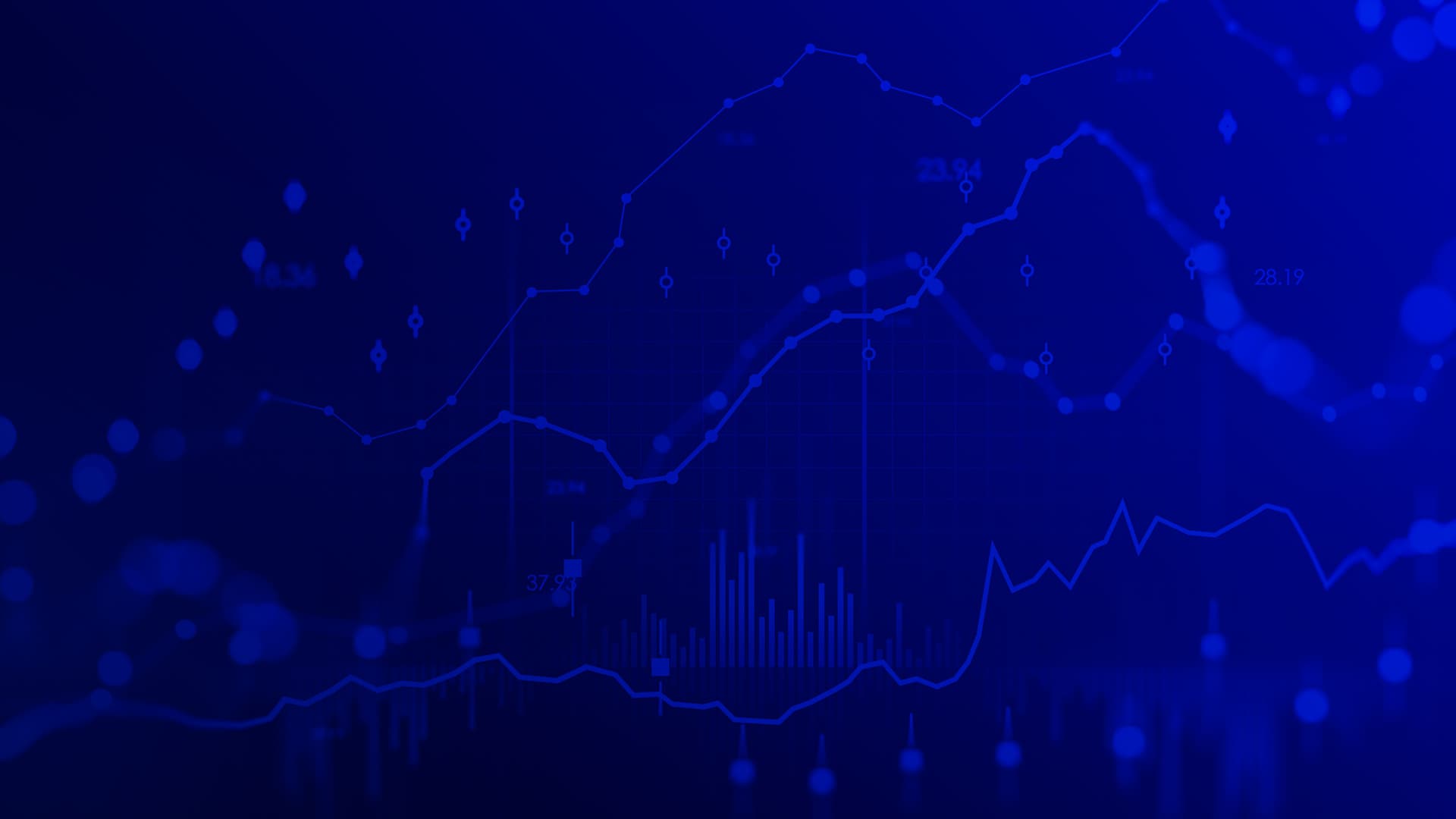
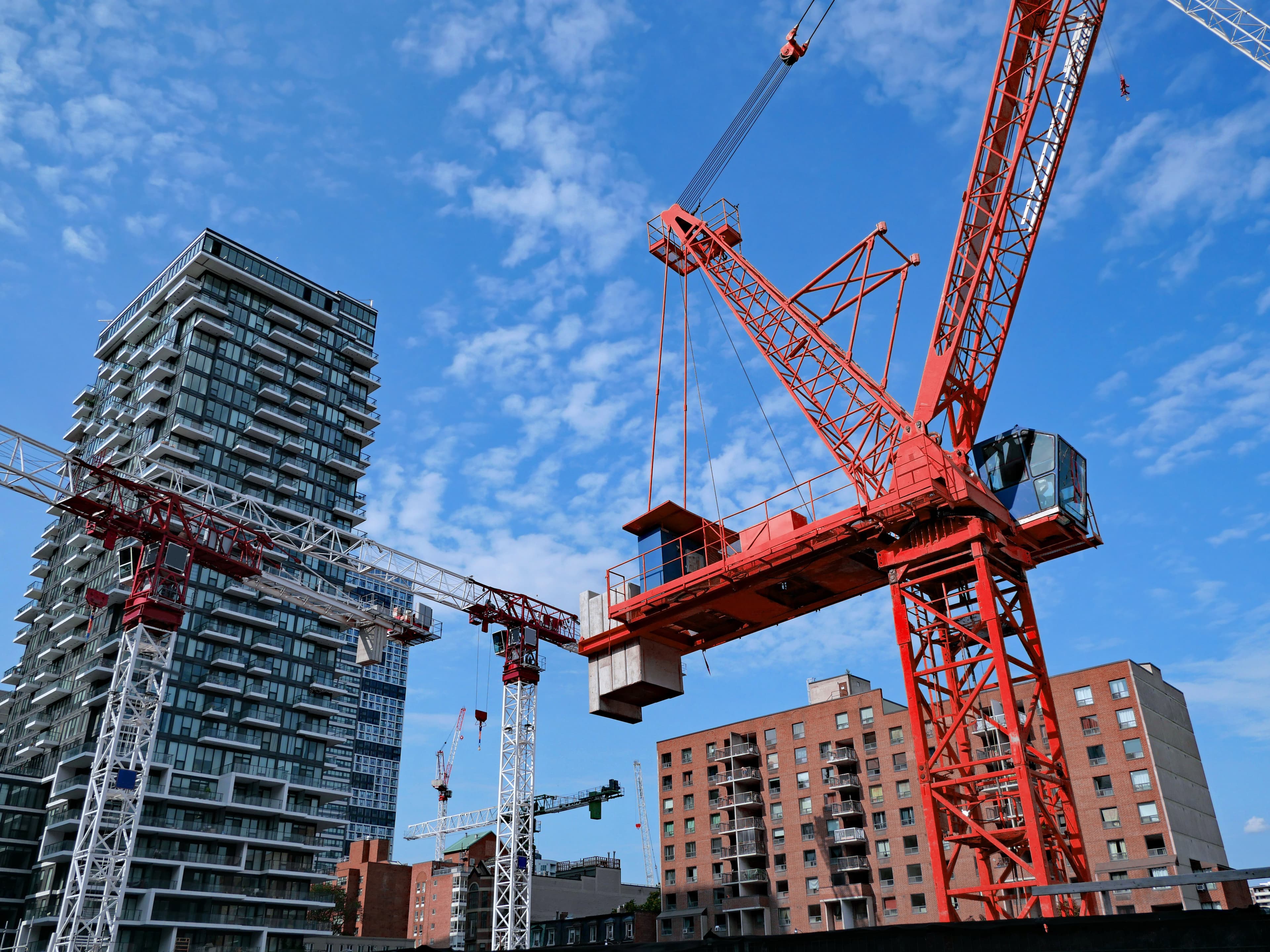
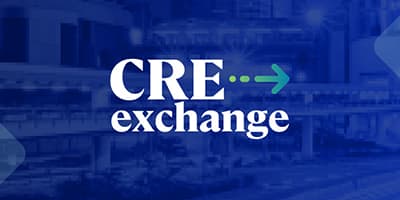
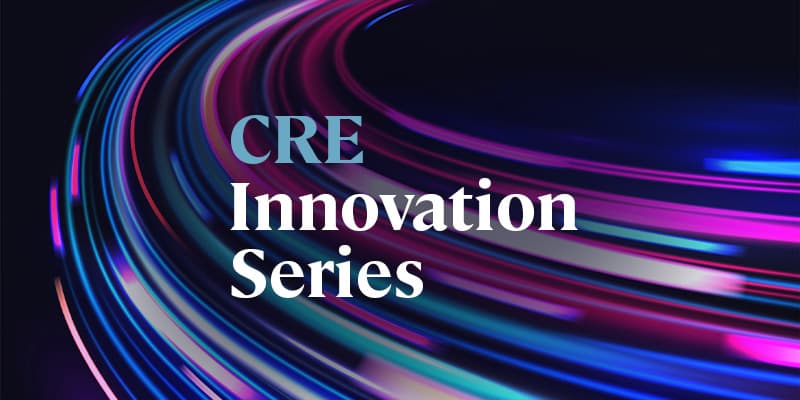
Trending articles
Featured insights
Australian construction price outlook - Q1 2025
Combining our market intelligence with robust data sources to provide the Q1 2025 quarterly Australian construction material price indicators for the construction sector.
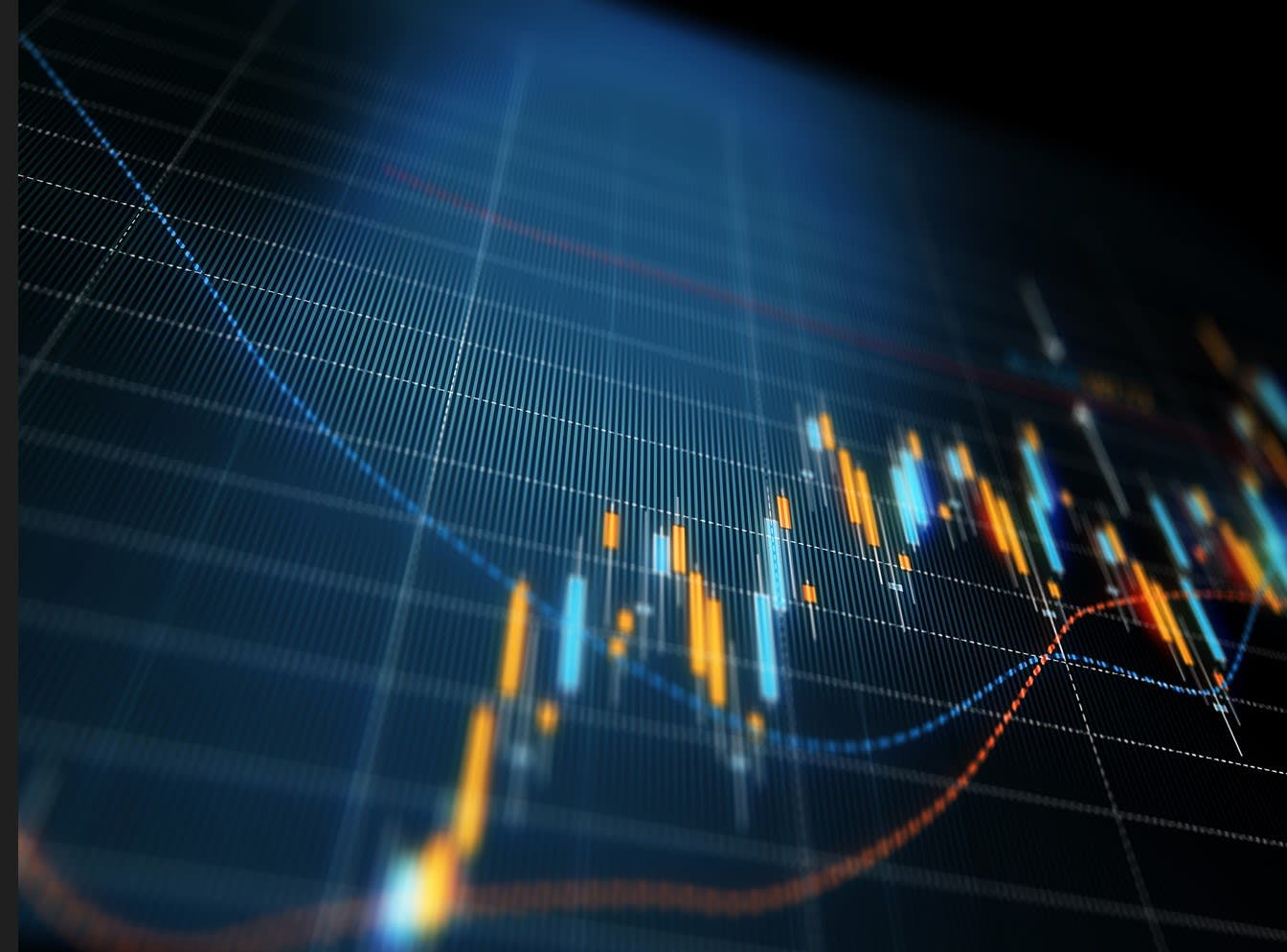
Featured insights
Canadian commercial real estate market update - Q1 2025
In our quarterly update on Canada's commercial real estate market, we discuss investment trends in Canada's five major markets: Toronto, Montreal, Vancouver, Ottawa and the Greater Golden Horseshoe.
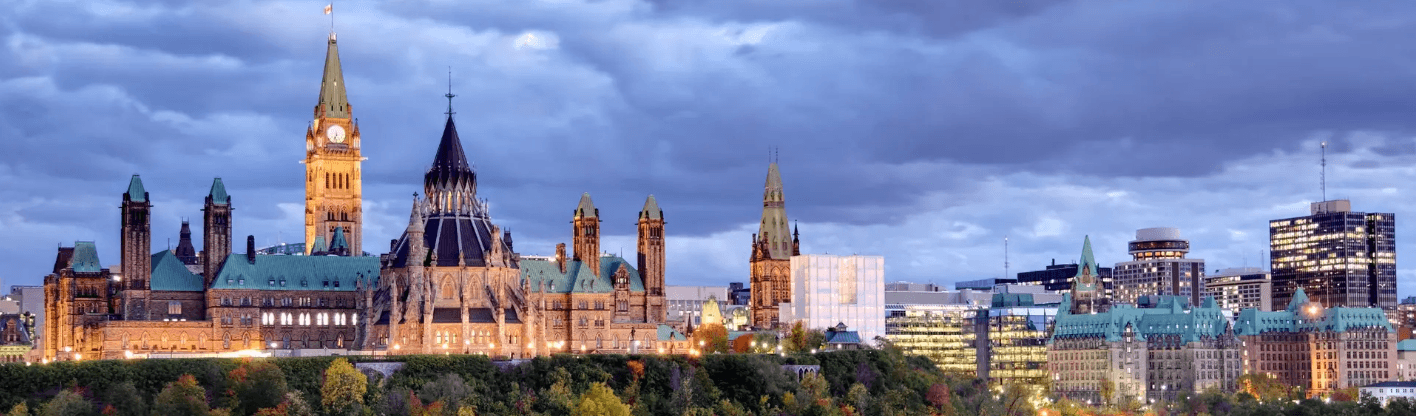
Featured insights
US commercial real estate transaction analysis – Q1 2025
A quarterly review of US commercial real estate transaction activity across all property types.
FEATURED episode
EP68 - Just how liquid is commercial real estate?
Dr. Philip English from Temple University joins us to explore commercial real estate liquidity, sharing insights from an upcoming joint research paper with Altus Group along with a broader discussion on how liquidity shapes investment decisions, the limits of traditional market metrics, and what new research reveals about true liquidity.
From transaction-based indices to the evolution of market structures, this discussion highlights the complexities and opportunities for investors and lenders regarding commercial real estate liquidity.
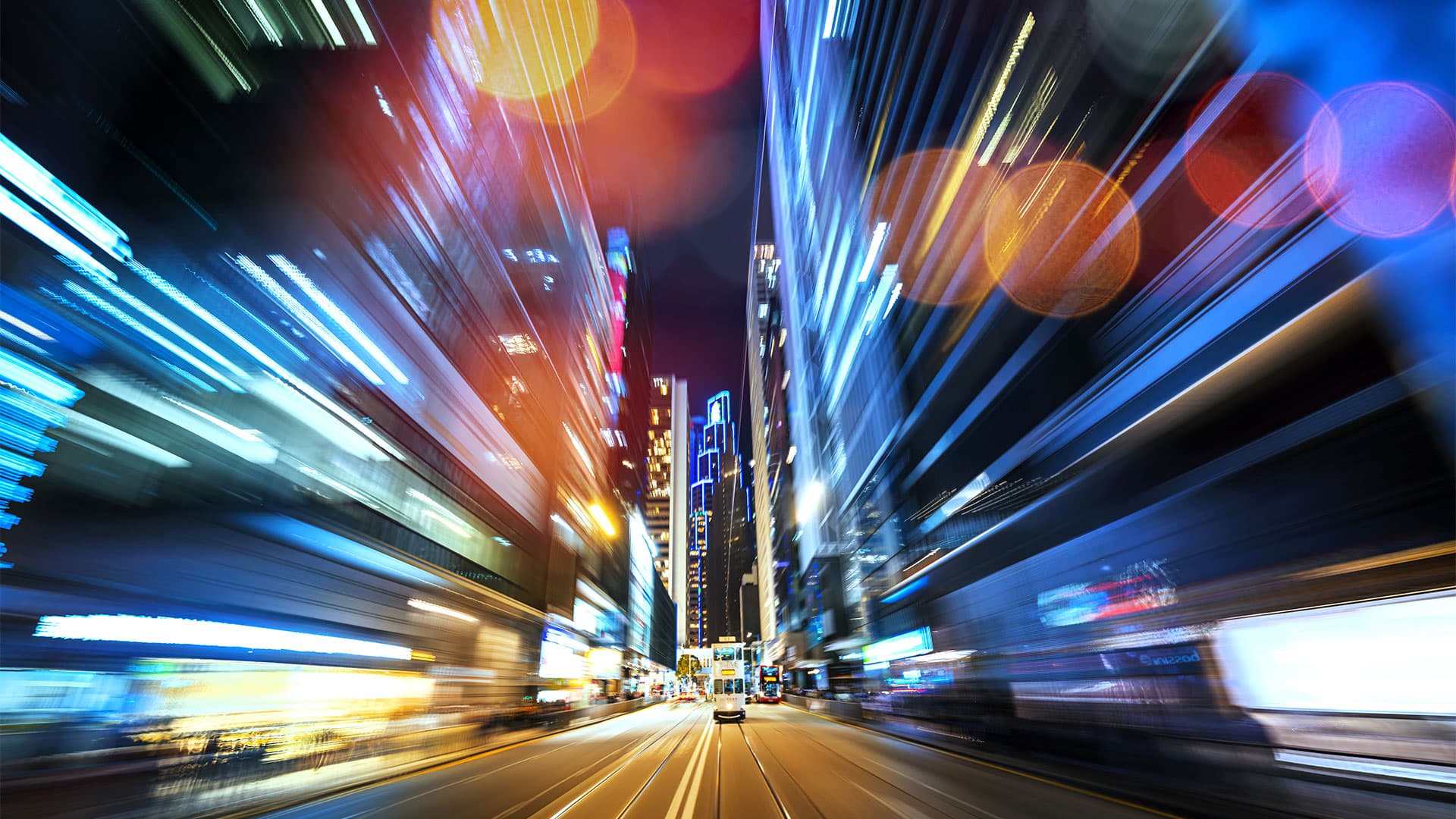