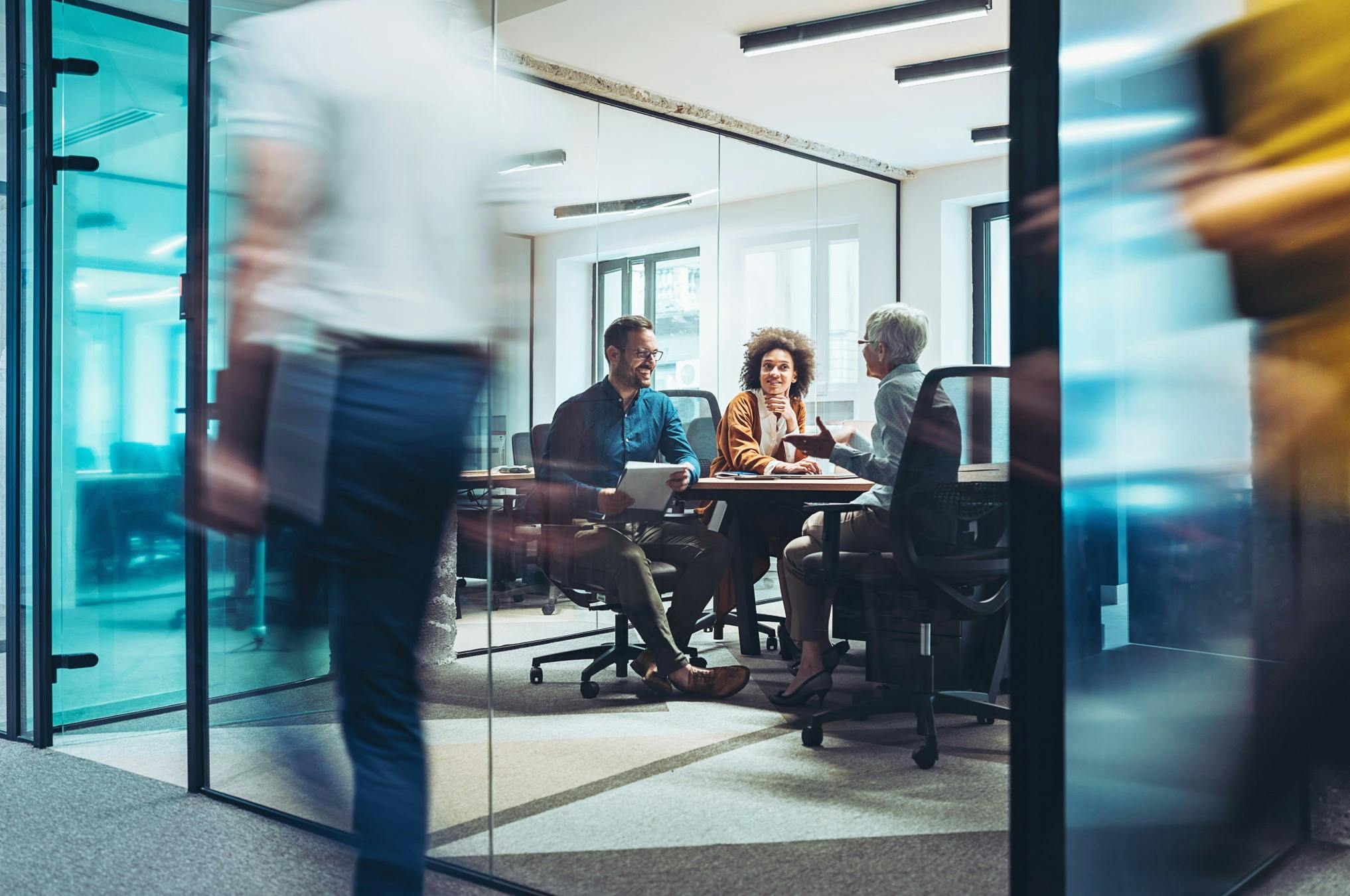
Commercial real estate consulting & advisory services
Make faster, smarter decisions backed by our unique offering of global expertise, a wealth of market data and leading technologies
Deep industry expertise, global reach and data-driven insights
Valuation advisory
Receive trusted and independent, ARGUS powered real estate valuations and appraisals for your commercial real estate investments.
Development advisory
Receive independent advice to manage construction costs better, mitigate financial risks and improve operational outcomes.
One11 Advisors
One11 Advisors is a trusted and independent advisor delivering strategy, operations and technology solutions for CRE companies.