In our previous article, Facilities maintenance 101, we explained the critical role of facilities maintenance in keeping deferral costs down and preventing premature building failure, and that what is most important is to ensure the right maintenance is carried out as effectively and efficiently as possible.
In order to achieve success in facilities maintenance, and effectively mitigate risk and improve outcomes, a business should always consider these seven keys:
Ensuring there is an appropriate asset management and maintenance strategy
Developing and executing a preventive maintenance plan
Allocating the appropriate priority to each task
Implementing the appropriate business tools to track and manage maintenance
Creating the appropriate business processes
Building the organizational structure to encompass staff capabilities
Ring-fencing lifecycle and maintenance budgeting in a single entity
1. Determine a maintenance strategy that aligns with the business need
It all starts with strategy. As the old proverb goes, “if you don’t know where you are going, any road will take you there,” and that is especially pertinent here. Maintenance as a business function is growing in importance and recognition to become a much higher business priority now than before.
The risks of not being able to function as a result of underfunding maintenance should now feed into the corporate risk register, and be a part of corporate strategy. Thus, a strategic asset management plan (SAMP) should be aligned with business strategy and integrated in the business planning process.
A SAMP is the first step in an integrated property portfolio and facilities management approach for acquisition, construction, operation & maintenance, optimization, renewal and, ultimately, disposal.
With the SAMP in place, distinct asset management plans can be developed according to the business need – system type, facility sector, geography, etc. Within those plans will be a variety of maintenance strategies applied to assets such as performance-based, predictive, reliability-centered, or condition-based. Even “run-to-fail” or reactive maintenance can form part of the strategy when the impact of failure is low.
2. Preventive maintenance planning that includes (costed) in-year, 3 to 5-year rolling, and lifecycle plans
It is important to determine what preventive maintenance needs to be carried out, and when then documenting it in a Planned Maintenance Program (PMP). Preventive maintenance will prevent early failure or reduced operating capability, avoiding more costly emergency, breakdown, or unscheduled corrective maintenance, and can reverse the trend of deferred maintenance. Research has also shown that preventive maintenance programs result in a significant return on investment, primarily from extending the useful life of equipment.
The asset management strategy should include in-year as well as short (i.e. 3-5 years) and long term (lifecycle) costed plans as part of the asset management plans, so future scenarios can be anticipated, no funding requests come as a surprise, and long range budget forecasting is embodied in the business.
3. Prioritize tasks to ensure the most critical and important ones are achieved first
Although task prioritization is part of the planning process in Key #2, we’ve identified it here as its own key. Proper prioritization is not only good practice; it is crucial in managing deferral in the light of budget cuts.
When faced with a multitude of tasks, the best way to get the most out of the maintenance budget is to prioritize them into sequential categories and work down the list using a risk-based approach, and analyzing “what-if” scenarios. A prioritization method like this gives justification to budget requests and also can demonstrate the impact of reducing the budget.
We recommend the following prioritization method – it’s simple, and a template like this will help you to give justification to budget requests and demonstrate the impacts of reducing the budget.
4. Leverage business tools that can provide quality data for analysis
Data is essential to making critical business decisions and many organizations don’t apply sufficient resources to the business tools or systems that can generate good quality data.
Critical cost and performance factors like productivity, speed of response and repair, task process improvement, inordinate maintenance costs, and many more can all be improved as long as they are measured and analyzed.
There are many tools in the market for maintenance management, workplace management, and energy management. What is important is that:
They are procured effectively to meet the business need
They are implemented properly
Effective processes are in place to guide the usage of the systems and ensure consistency (see Key #5 below)
Staff are adequately trained to use the systems (see Key #6 below)
There are business functions established for work control and analysis
Having determined what tasks need to be carried out and in what priority, a well set up maintenance management system will help with eliminating wasted time, and through a continuous improvement process, allow for effective and efficient work.
5. Implement business processes that promote efficiency and productivity
Having the tools or systems in place and the staff to carry out the tasks it generates is one thing, but if the right processes are not in place, work will either be missed or time will be wasted, and result in incomplete and inaccurate data.
From keeping the asset register up to date, to stopping a technician from trying to maintain something that no longer exists or performing maintenance on new equipment that hasn’t been entered, to analyzing the most cost-effective risk-based approach to lifecycle replacement – all processes are essential to effective operation.
How do work orders get completed? How is time allocated? How are materials or spares purchased? What spares are kept in stock, at what level, and which ones are deemed critical? How are tasks charged from inventory to the work order, and at what cost? These are a few of the questions that must be addressed through process; indeed, every planned maintenance task is also a process and subject to regular review (how can it be done more efficiently?).
Getting the best out of the systems needs guidance and consistency through process.
6. Optimize organizational and workforce capability
Not only does the workforce need the skills to carry out the work, they also need to be able to control and analyze the work. Staff capability should not stand still (as systems don’t and procedures shouldn’t), and the organization should provide training plans to develop, enhance, and motivate. The following should be considered when assessing the workforce needs:
Technical skills, trade qualifications, and experience that match equipment needs
In-house vs sub-contractor delivery (for instance, what is too specialized to carry in house?)
Understanding priorities determined by criticality of equipment and impact of downtime
Interpretation of data and forecasting of intervention
The last bullet is a very important part of the capability of any maintenance organization – knowing what the system can do and analyzing the data in order to make continuous improvements to processes and tasks.
7. Establish a single entity for asset management
Asset management will be more effective if the funding for maintenance and lifecycle is carved out of the operating and capital budgets before other priorities are dealt with, so that maintenance is treated in totality.
It may even warrant the establishment of a “third budget” – the total maintenance budget, or as explained in ISO 55010, “TotEx” (TotEx = CapEx + OpEx), including utilities for energy management purposes. The TotEx should then be separated and ring-fenced from regular operational and capital expenditures.
This is exactly what happens during the operating period of a Design, Build, Finance and Maintain (DBFM), arguably a gold standard in asset management. However, for non-DBFM, this will only make sense if there is a single entity responsible for all three components – lifecycle, maintenance and utilities should all come under the responsibility of a single asset management organizational entity.
Pulling it all together
Being able to effectively mitigate risk and improve outcomes relies on careful strategy, planning, and prioritizing. The appropriate tools, an organized and capable team, and functional governing processes need to be mutually supported in order to execute it all efficiently.
Ultimately, aligning your maintenance and lifecycle budgets and separating them from other operating and capital is imperative to success, and by designating asset management as a single entity, you can ensure accountability for maintenance, lifecycle, and energy management, and safeguard your facility against future failure.
Want to be notified of our new and relevant CRE content, articles and events?
Author
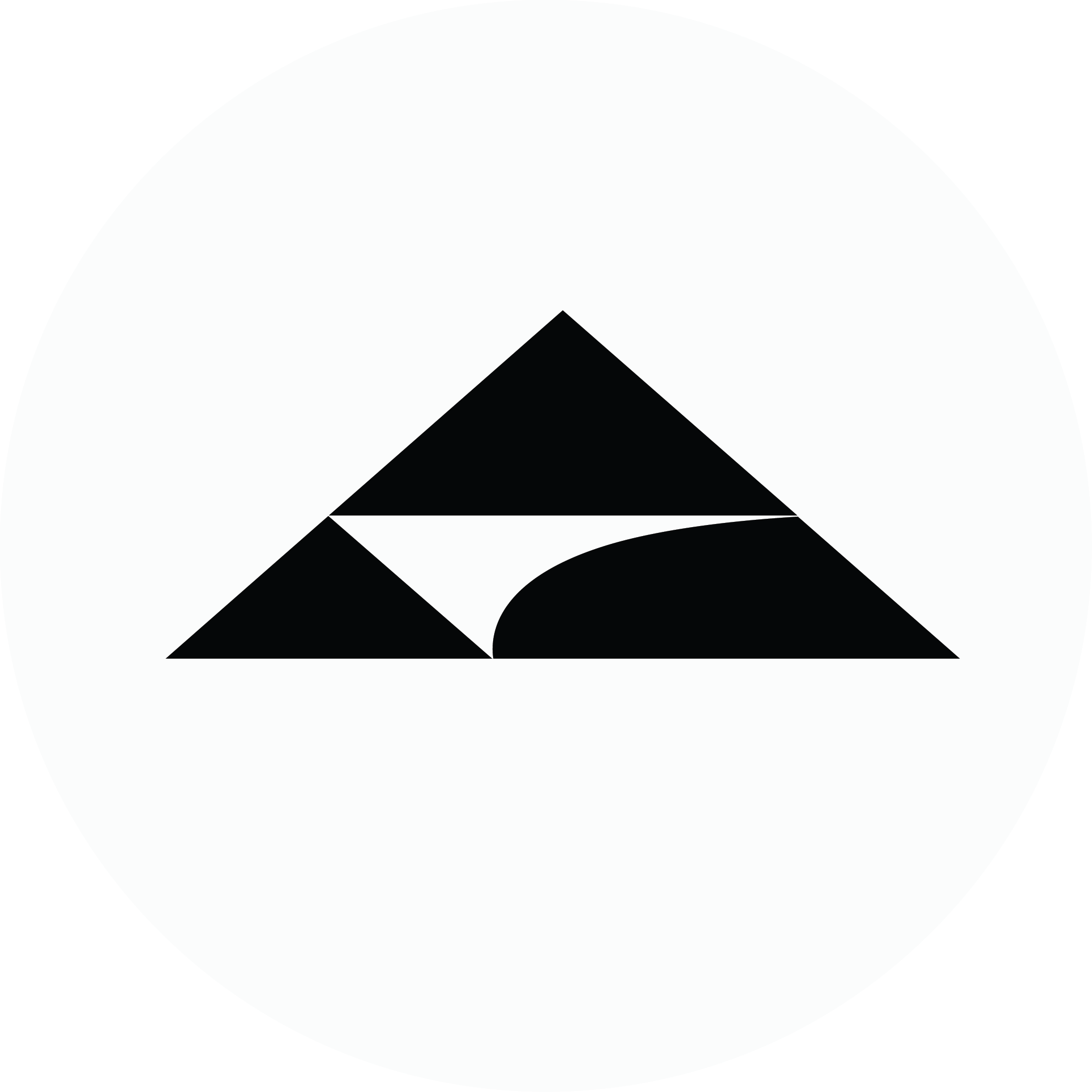
Altus Group
Author
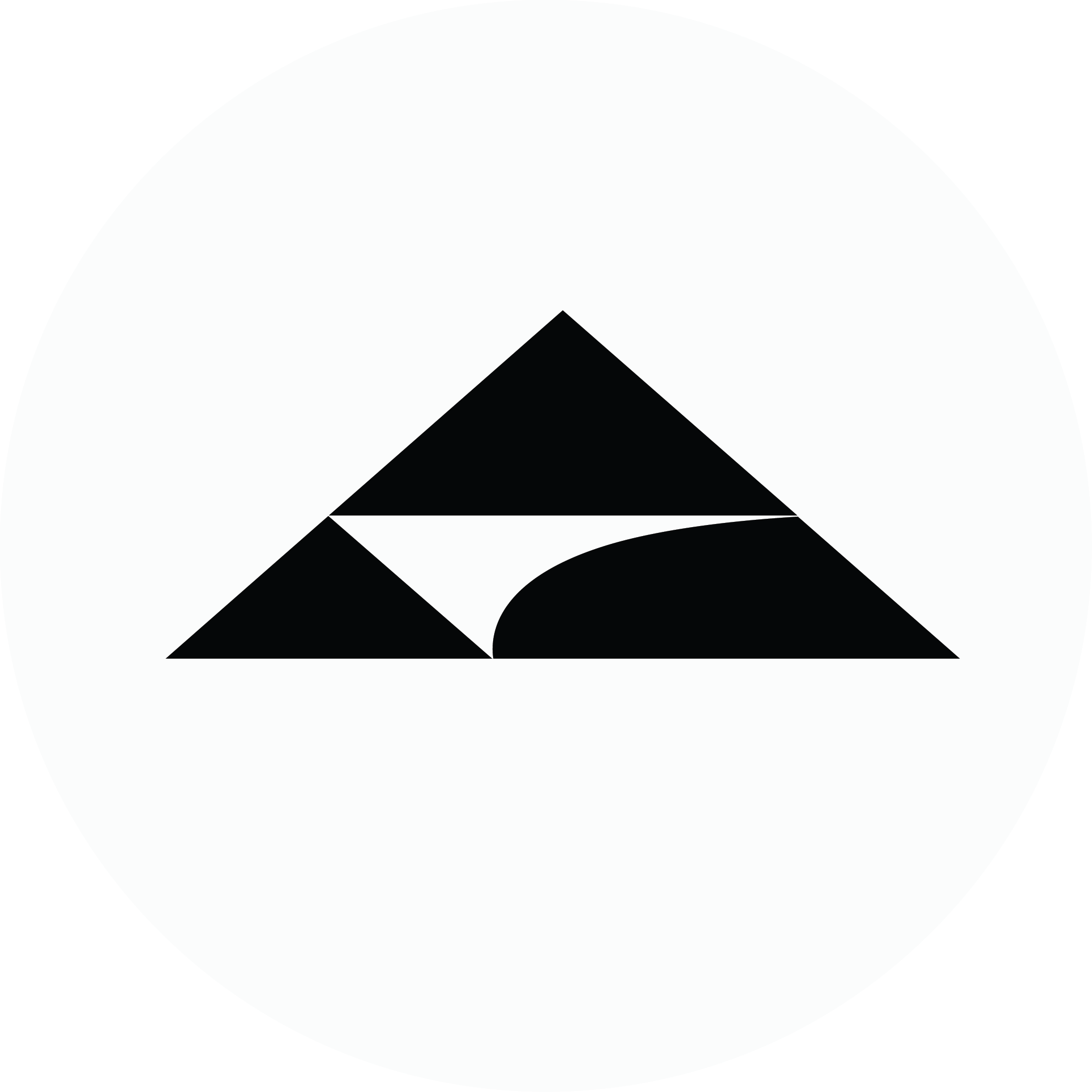
Altus Group
Resources
Latest insights
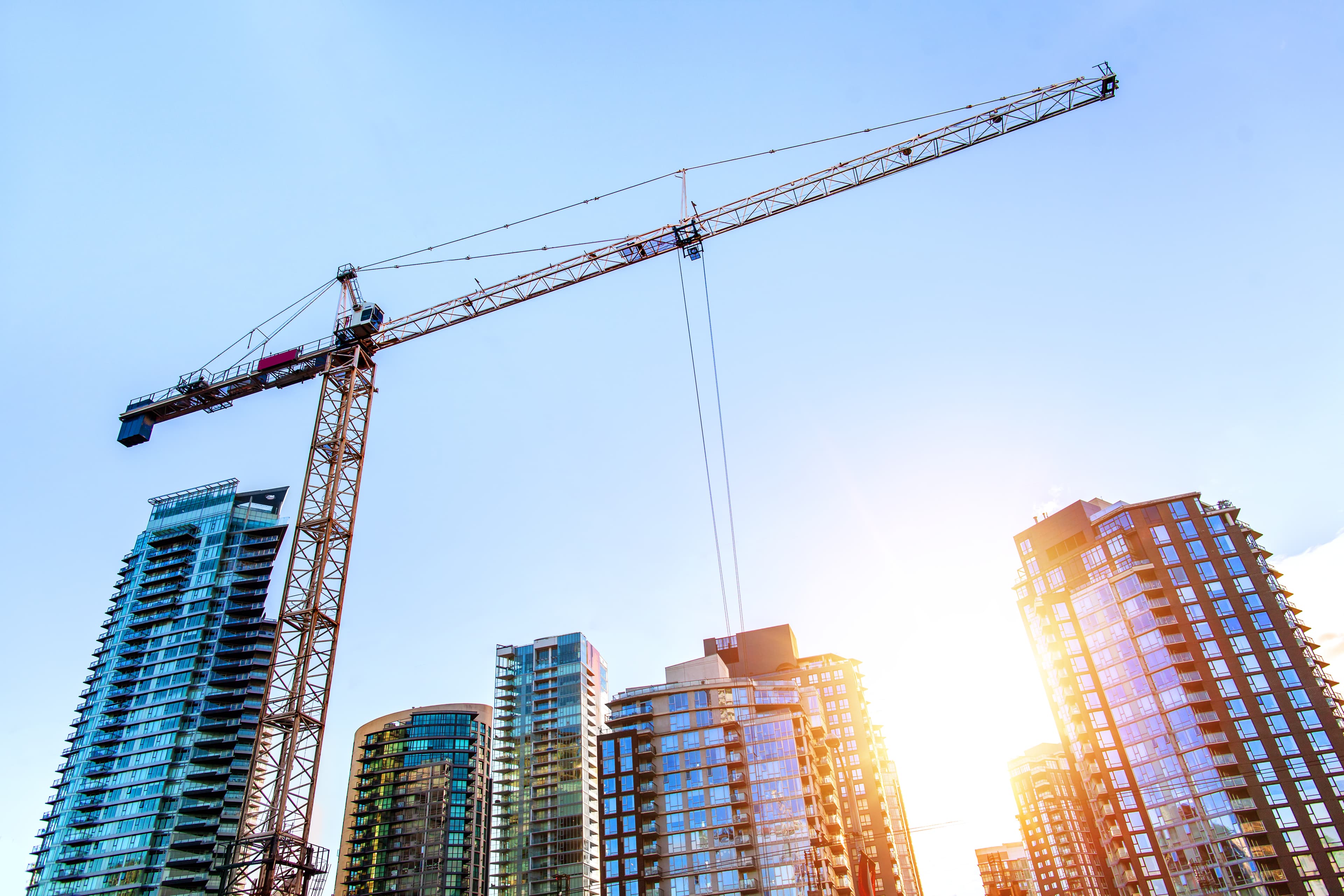
Mar 27, 2025
2025 Canadian Cost Guide: Costs are stabilizing despite looming threats on the horizon
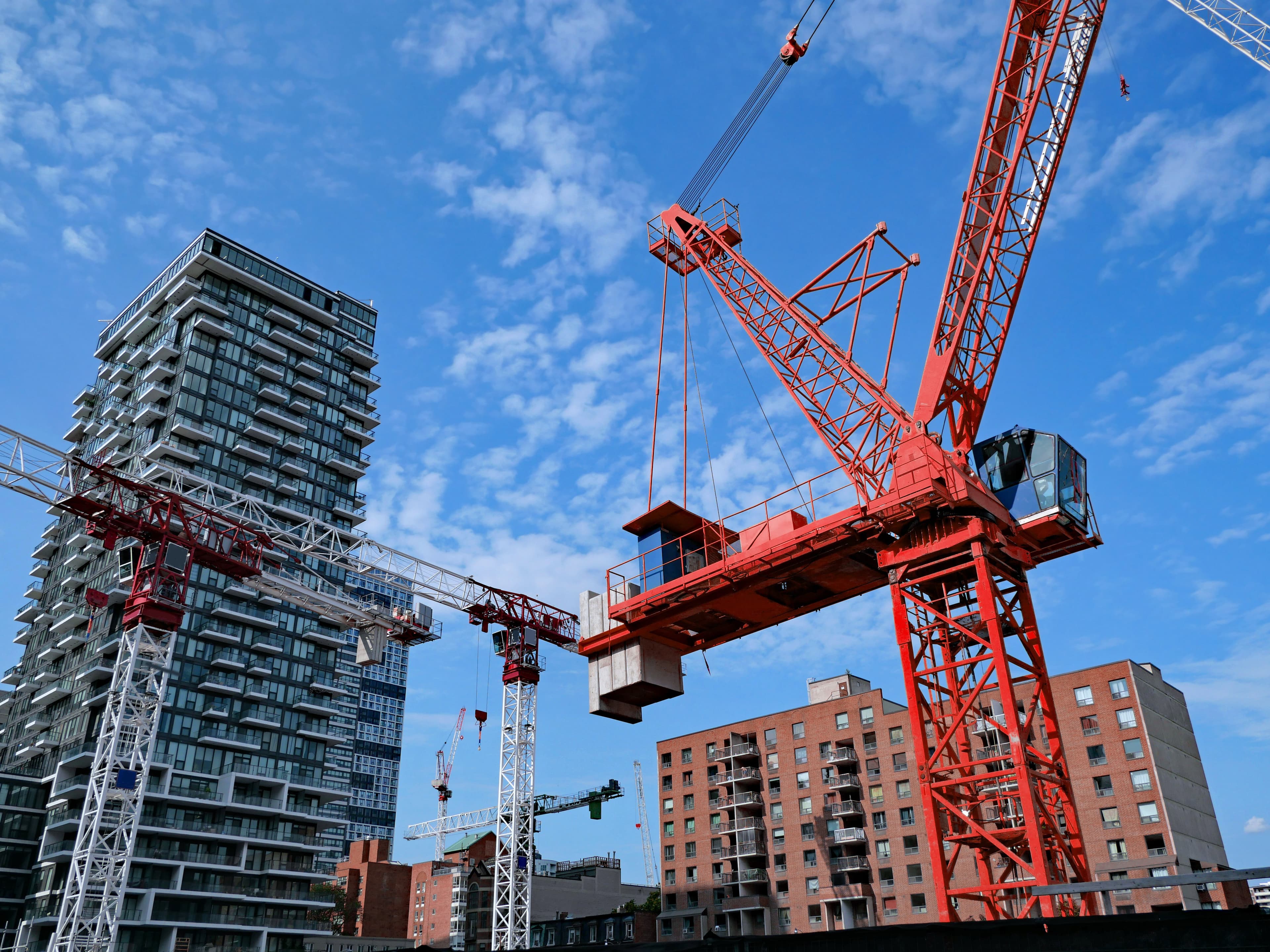
Jan 22, 2025
Building solutions - The impact of CMHC loans on Canada's rental development efforts
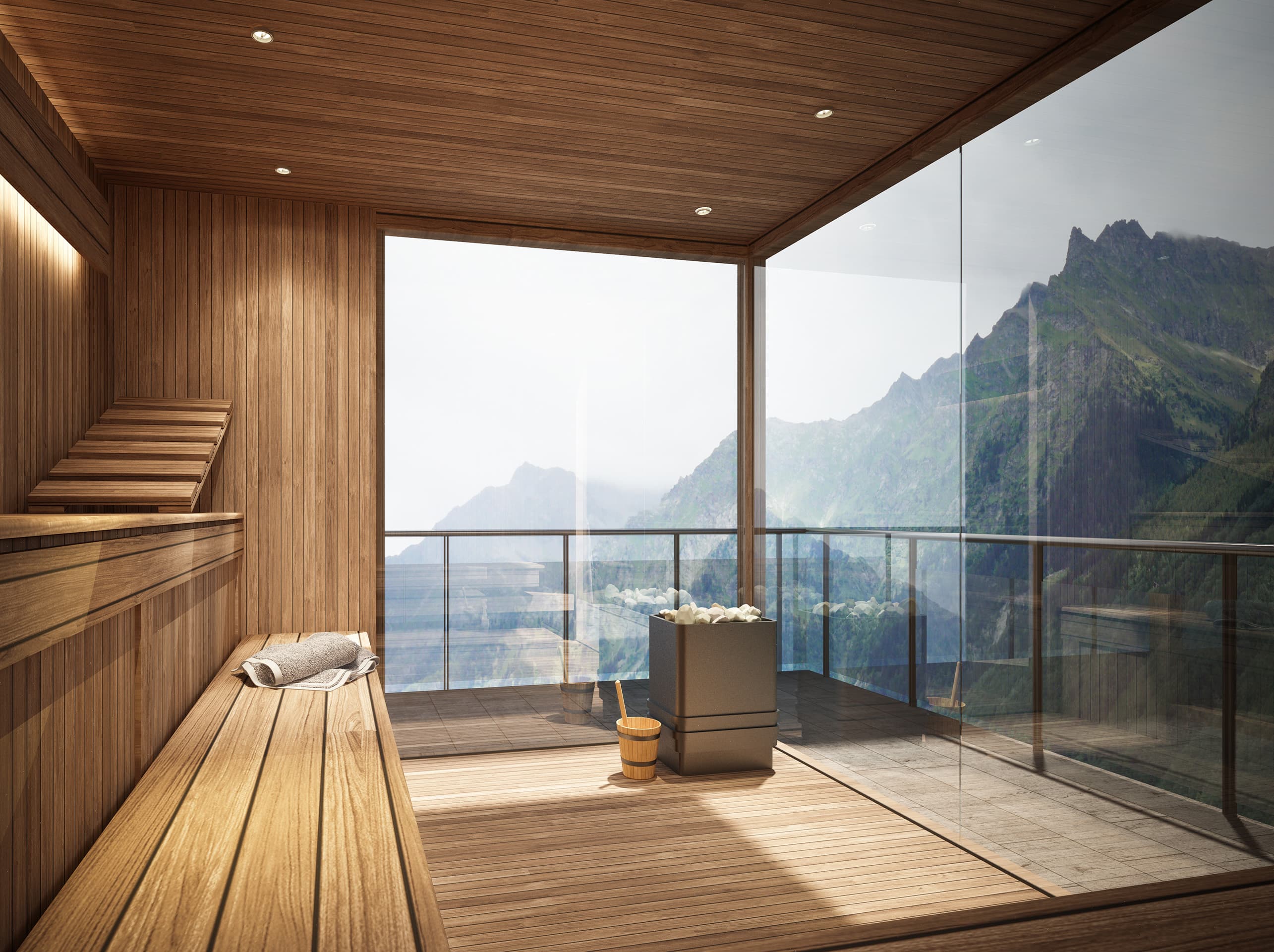
May 16, 2024
Progressive Design-Build provides notable advantages for today's complex P3 infrastructure projects
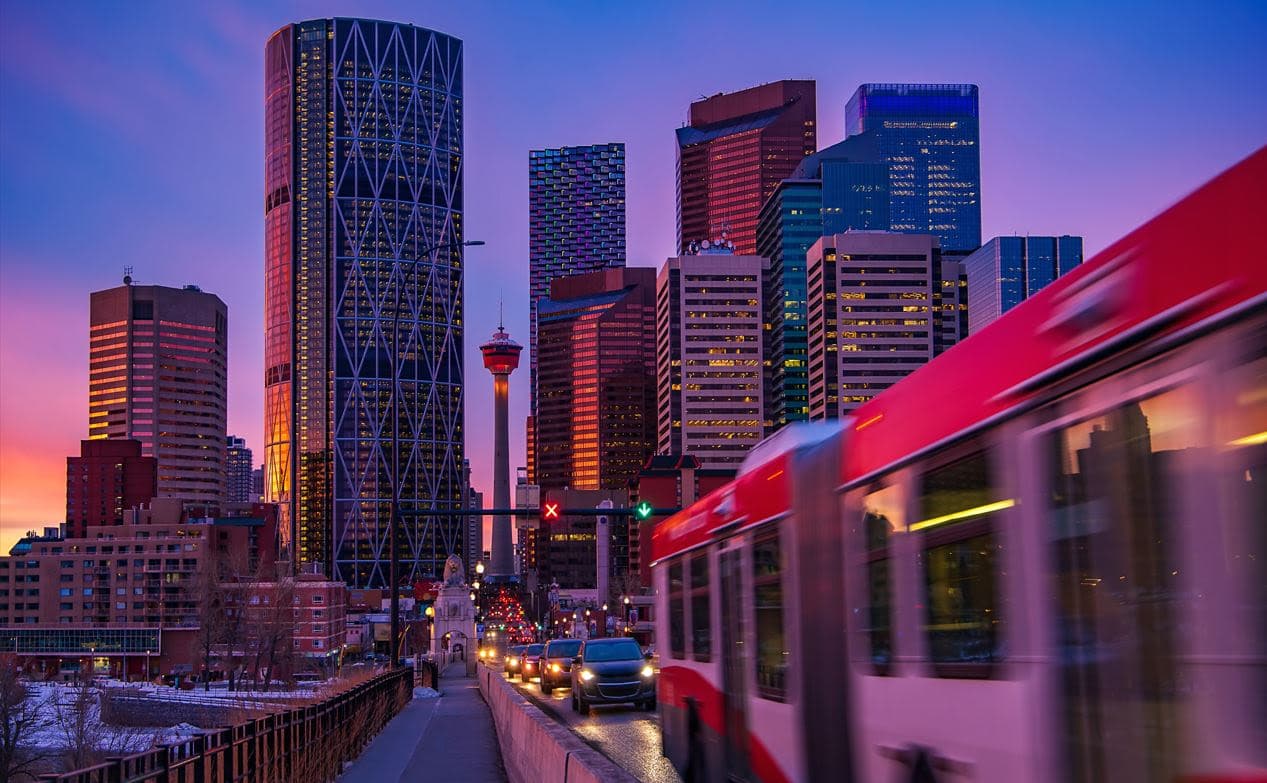