Nothing turns heads in the construction industry and quantity surveying circles quicker than the phrase “cost escalation”. Everyone wants to know what’s in store after two years of rapidly rising prices.
Covid-19 disrupted global production and supply chains, but the pandemic is just one factor driving up prices. Extreme weather, from wildfires to winter storms in the US, shuttered factories and bankrupt property behemoths in Asia, emissions-reduction policies in Europe, local labour shortages and even the Suez Canal blockage all contributed to skyrocketing costs. Escalating costs and lengthy delays have caused some projects to go well beyond budget. While unprecedented fiscal stimulus initially led to a drop in insolvencies across Australian companies, it is anticipated that there will be a significant increase in insolvency appointments as discussed in our early article “It’s about to get messy: Can you spot the yellow flags on your construction project”.
With so many factors at play, how do cost managers and quantity surveyors come up with a headline figure? To find out, let’s unpack some of the factors influencing cost escalation in 2022.
Interest rates
First and foremost, there are interest rates. While the Australian cash rate remains at an all-time low of 0.1%, financial markets have priced in four rate hikes in 2022. Reserve Bank of Australia governor Philip Lowe says a rate rise in 2022 is “plausible” following growing inflation, falling unemployment and a faster-than-expected economic recovery. With US inflation hitting 7% – a fresh high since 1982 – it is only a matter of time before the US Federal Reserve lifts its rates, and this will force Governor Lowe’s hand.
The price of many of our most common construction materials – steel, plastic, copper and glass, to name a few – are all hedged to the US dollar. So are freight costs, which escalated at an eyewatering pace in response to surging demand during Covid-19 lockdowns. Shipping a 40-foot container from Shanghai to Sydney more than doubled last year, and experts predict spiralling freight rates will continue well into 2022.
Material shortages
While shortages appear to be easing, some materials are still in short supply. Take the squeeze on timber, which saw some builders waiting up to 26 weeks for supplies in 2021. While 80% of our timber is locally sourced, the balance comes from countries that slowed production in response to Covid.
Other factors are influencing the availability of product. The embattled Evergrande in China is just one example. Once the world’s largest property developer, Evergrande is struggling to repay a growing list of creditors more than $300 billion. The ripple effects will be felt as far away as Australia, as the viability of many Chinese suppliers is dependent on calling in Evergrande’s debt.
Sector growth
Costs are rising at different rates depending on the sector. Many developers made the pivot to industrial projects in 2021 and demand for sheds soared. But so did the cost of the material with which they are built, as steel prices surged by as much as 200% in 2021.
Similarly, Australia now has the fastest-growing data centre market in the Asia Pacific, with space under development expected to nearly double over the next few years. But data centres are constructed with materials, notably steel and copper, that hit all-time price highs in 2021, not to mention mechanical equipment that must be freighted from far-flung locations.
Rising interest rates may cool some residential markets, especially cities like Sydney, Melbourne and Canberra where median house prices now exceed $1 million. But cost inflation in the residential sector is as much a question of building quality.
State building commissioners are turning up the heat on building defects. As just one illustration, NSW Building Commissioner David Chandler recently forced a developer to tear out and re-tile more than 150 bathrooms that failed to meet the standard. Stories like this are shrinking the pool of contractors prepared to take on the risk in residential projects.
Labour shortages
Having turned off the migration tap two years ago, skills shortages across the construction industry are also hitting budget bottom lines. NAB’s labour analysts say around 40% of all Australian businesses are feeling Australia’s talent squeeze, but tradespeople account for around 35% of the nation’s total workforce shortage.
We have traditionally topped up our labour pool with overseas talent, but Australia’s unemployment rate isn’t the only one at an all-time low – many other nations are also in stiff competition for labour.
Piecing together the project pressures
How do we make sense of all these underlying inflationary pressures to cost a project?
The simple answer is that costs are heading into higher single digits. But just as every building is bespoke, so too is the cost estimation schedule. Construction projects are complex, bringing together as many as 40 different trades and many moving parts. No headline figure can capture the nuance of cost escalation.
When will cost escalation reach its peak? Altus Group expects costs will continue to rise over the first half of the year before the impact of interest rate rises starts to slow the market.
The danger for the development industry is clear. In a fast-rising market, businesses can fall for the trap of thinking that a single figure will solve their problems. But if they can’t stay on top of price hikes, they run the very real risk of distress.
In a constantly changing market, one factor is consistent: the need for good advice relevant to the sector and building type. This is the fail-safe way to establish a robust budget and ride the waves of 2022.
Author
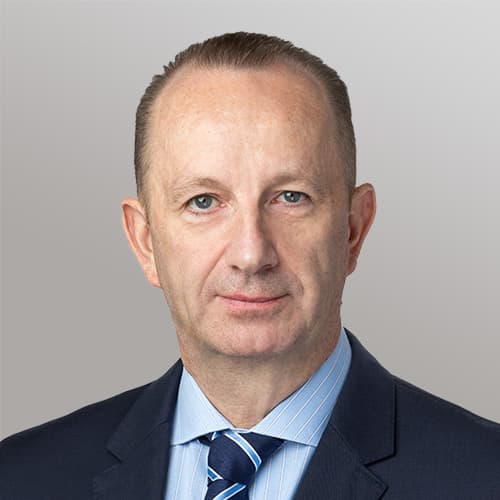
Niall McSweeney
Head of Development Advisory, Asia-Pacific
Author
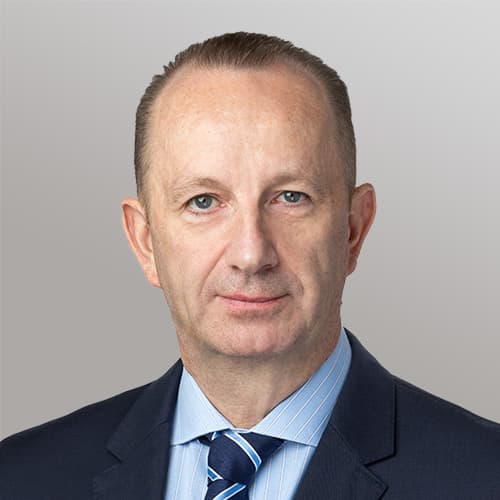
Niall McSweeney
Head of Development Advisory, Asia-Pacific
Resources
Latest insights
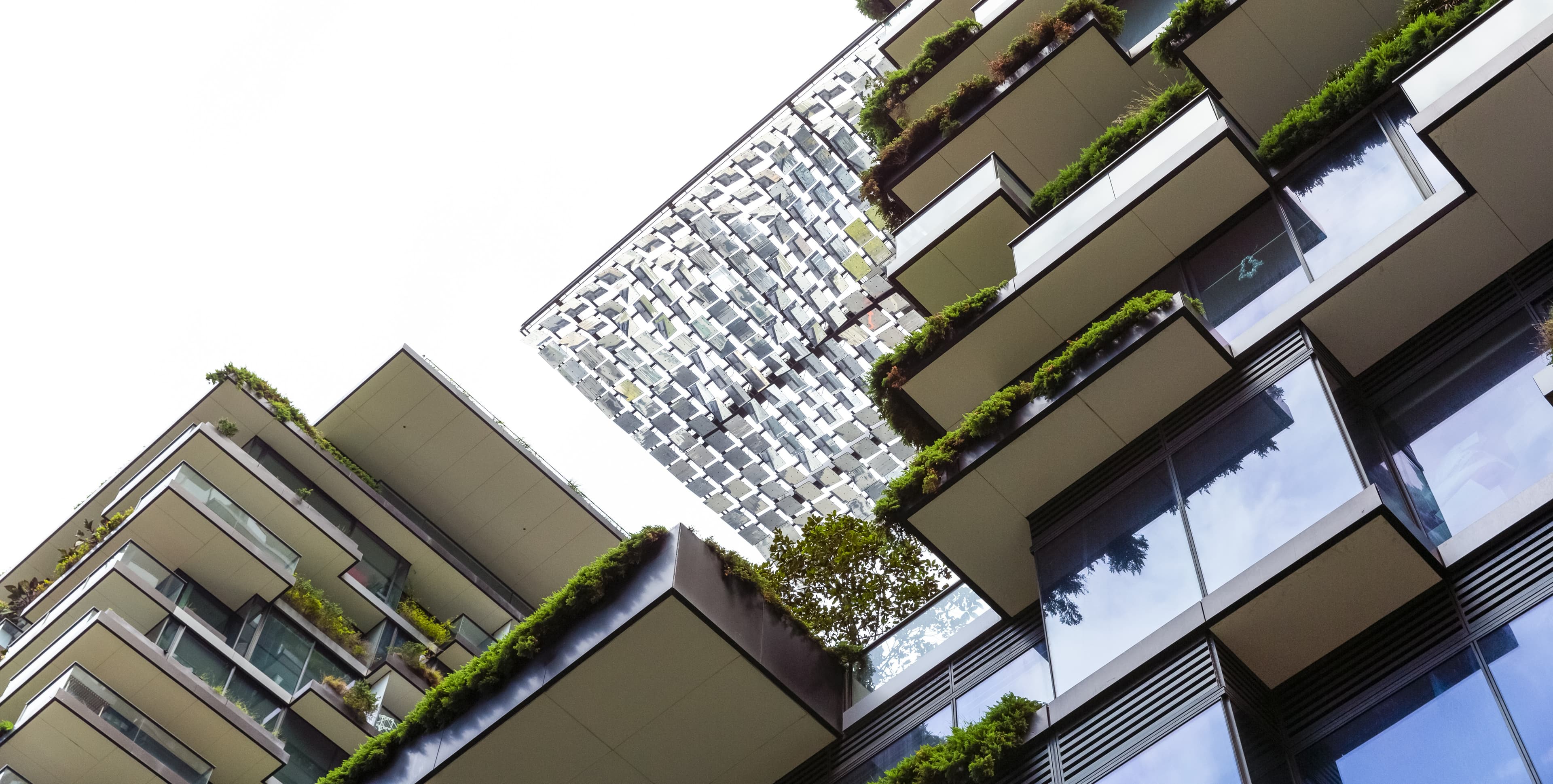
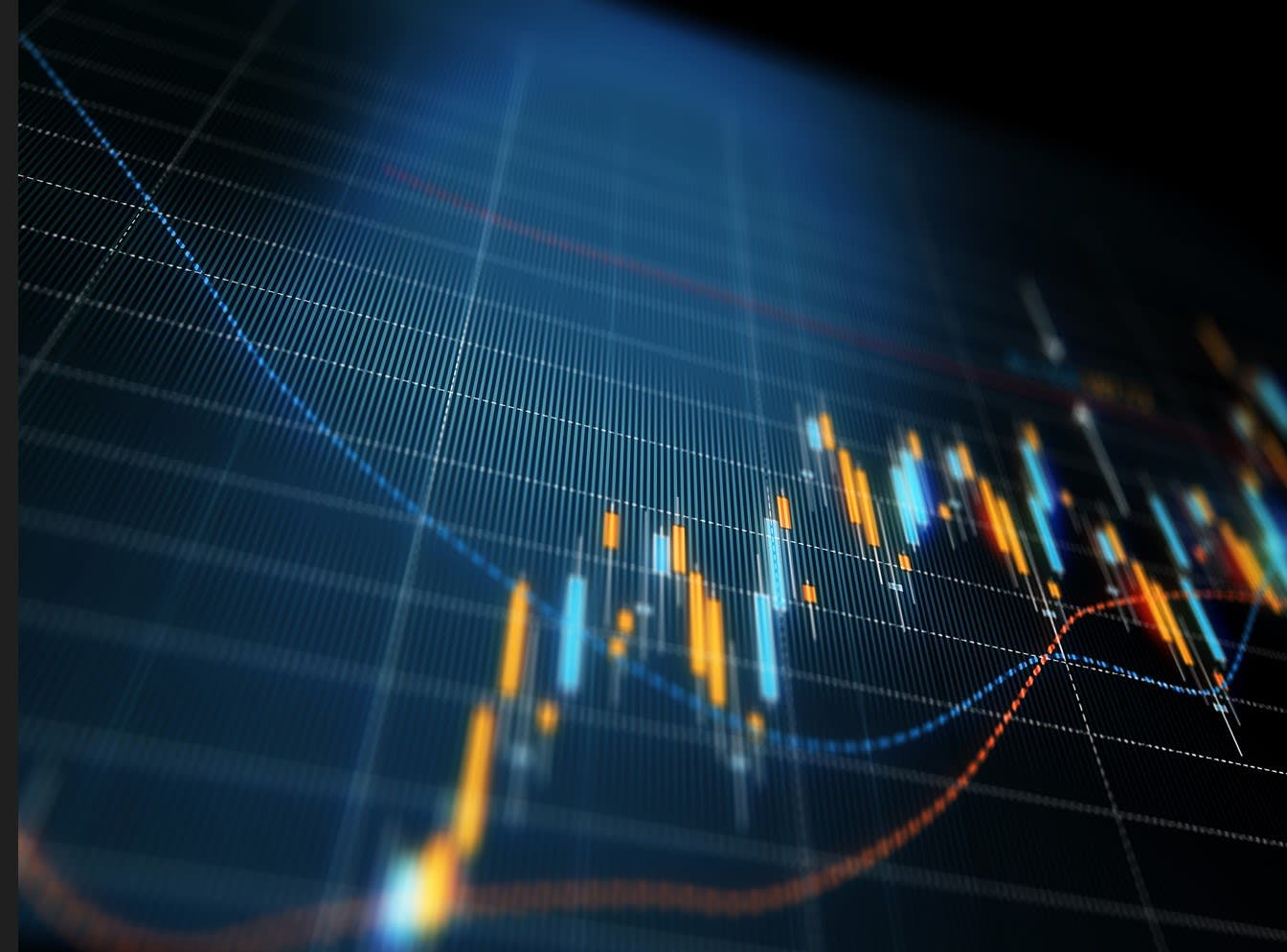
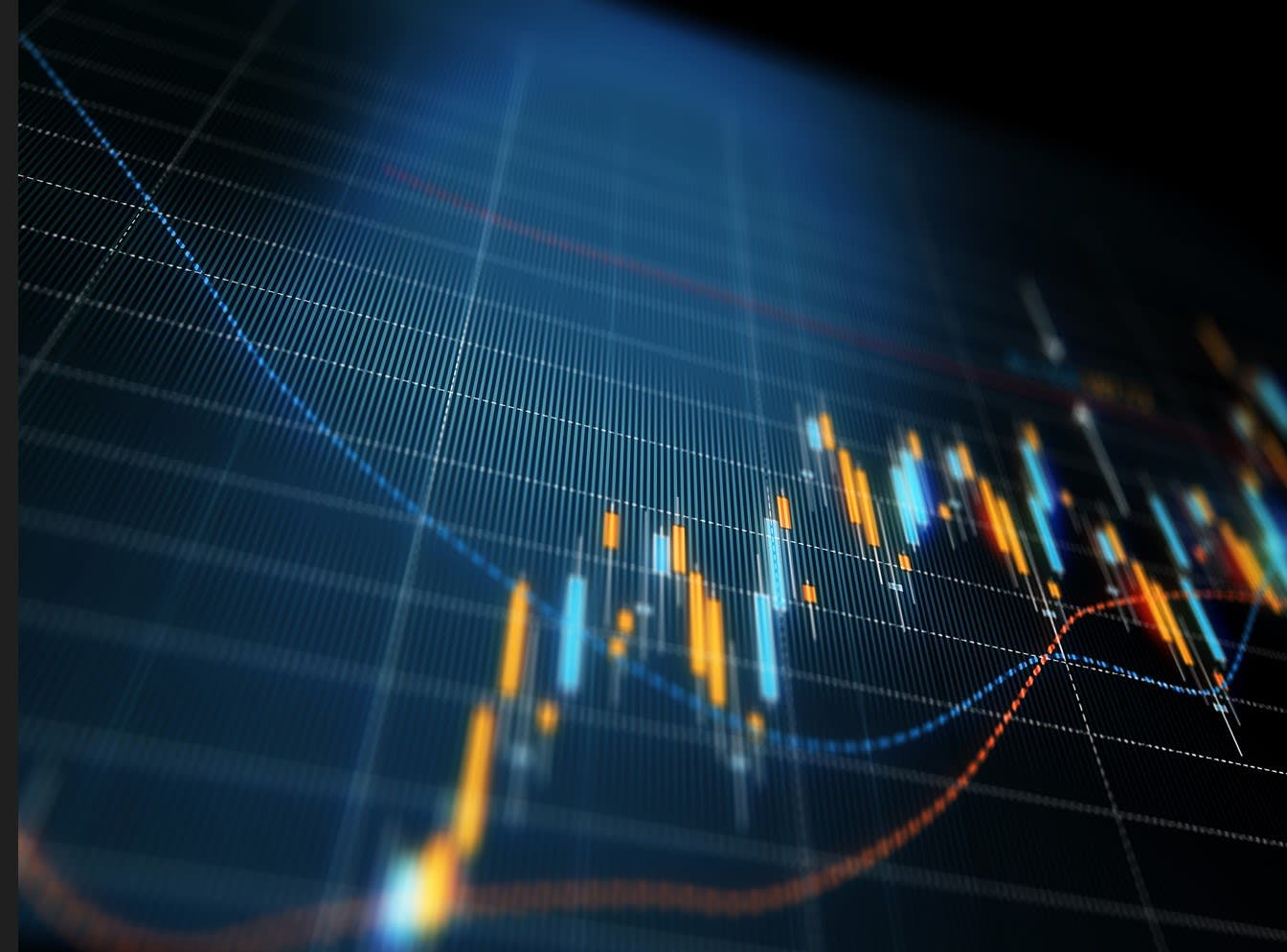
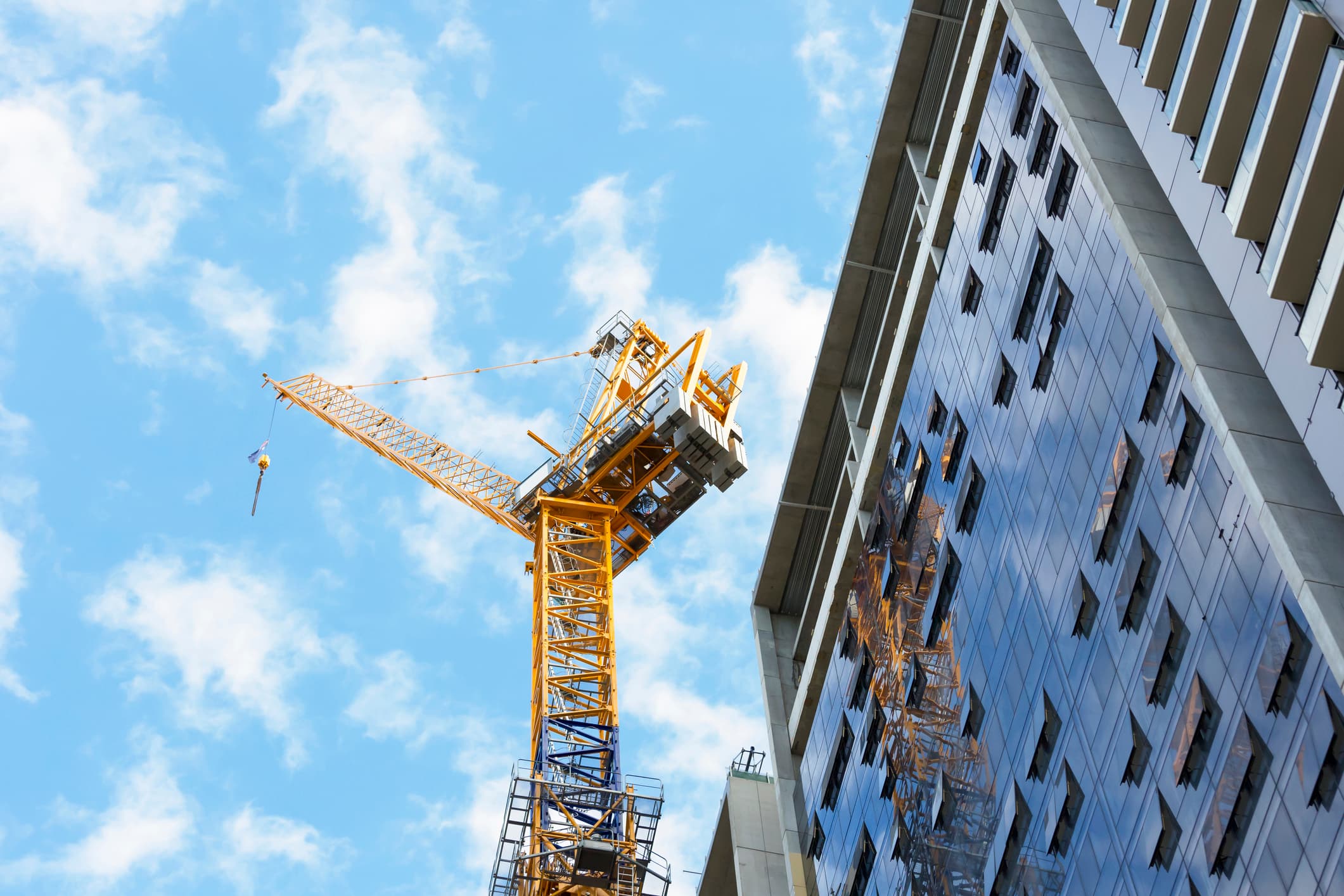
Jan 9, 2025
Building the future - Key trends shaping Australia’s construction industry in 2025
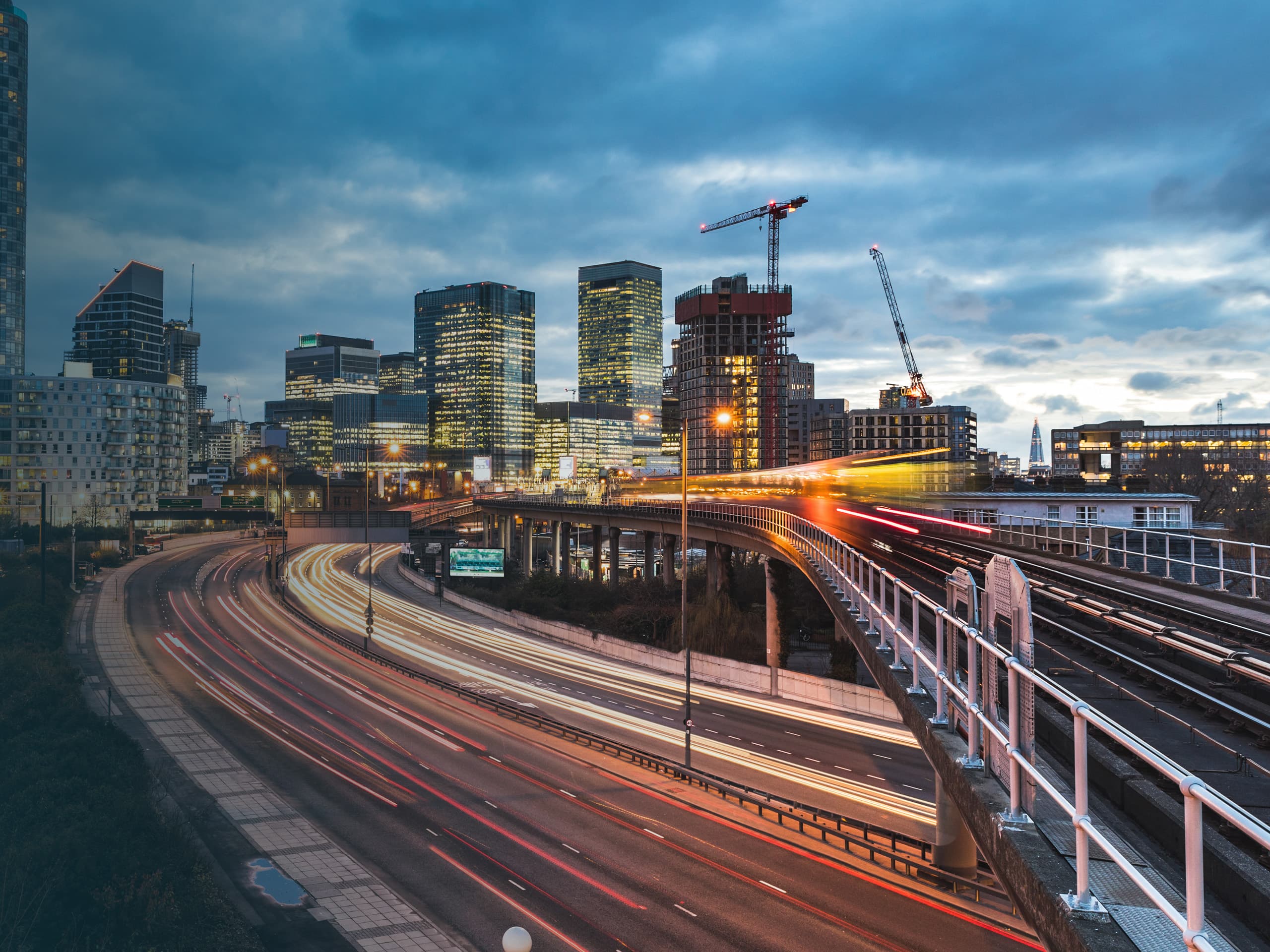