Modular and prefabrication hold the promise of faster production and lower cost construction. But is this always the case? In this guide, Altus Group weighs up the obstacles and opportunities.
What is modular construction?
Prefab, DfMA, off-site construction and modular are just some of the terms used describe the production of a building in a factory setting. So, what do they all mean?
Modular, 3D or volumetric construction: Entire modules, such as rooms, pods or even homes, are manufactured and assembled in a factory and then delivered to a site for installation. A building may be constructed entirely of modules, or portions may include conventional construction. Modular buildings may be wood, steel, concrete, or a combination, and as many stories as building codes allow.
Prefabricated (prefab) construction: Any component of a building – flat or modular – that is manufactured in a factory and then transported and installed on a building site.
Design for Manufacture and Assembly (DfMA): This combines the manufacture of building components, such as wall systems and façades, in a safe, clean and efficient factory environment, with on-site construction assembly. Essentially the product is a ‘kit of parts’ that is designed for ease of manufacture and assembly.
Panelised construction: Flat panels such as walls, floors and ceilings are manufactured in a factory and then transported and assembled onsite to form three-dimensional spaces.
What size is the modular construction market?
The modular construction and prefabrication market varies from country to country. But each market shares one characteristic: growth.
One recent report predicts the global market for modular and prefabricated construction will surpass US$200 billion by 2027. Another suggests the prefabricated homes market will reach US$153.7 billion by 2026 – a compound annual growth rate of 6.4%.
Some countries, like the United States, China and the countries of Scandinavia, have well established modular markets. Others, like China and Canada, are in their start-up phases.
What does best practice look like for modular construction?
Modular marvels are being constructed all over the world. Here are just a few inspiring examples…
Residential: The 135-metre-tall Ten Degrees Croydon in South London – currently the world’s tallest modular residential tower – features 546 homes in a pair of 38 and 44 storey towers. A variety of modern construction methods were employed, including virtual reality and 3D printing for rapid prototyping of the angled modular façade.
Residential: Australia's 323 La Trobe Street apartment tower rises 133 metres above the Melbourne city centre and tops out at an impressive 44 levels. The main structure for the $95 million high-rise was completed in eight months, twice as fast as a traditional build. Featuring modular bathroom pods, precast concrete slabs and pre-attached windows manufactured by off-site.
Single-family: IKEA and Skanska have teamed up to produce sustainable, quality, low-cost prefabricated homes under the banner of BoKlok. More than 14,000 homes in Sweden, Finland, Norway and the UK have been delivered using a model that costs around 40% less than traditional construction and is delivered in eight to 12 months.
Education: Constructed in 2017, Murray Middle School in California incorporates 68,000 sf of permanent modular buildings – from standard classrooms to science labs, a music and art building to a media centre, a library, gymnasium and administration building. The school’s multi-purpose building features anti-terrorism “blast force” design. The entire project was completed in just 319 days.
Healthcare: In Victoria, Australia, the state government has used three modular construction methods for the Northern Hospital, Sunshine Hospital and The McKellar Centre. At the McKellar Centre, for instance, a “cold shell” approach – where the structural steel frame, façade elements and roof were built offsite, and the internal fit out elements completed onsite – meant main contractor Lendlease could install 137 modules in just eight weeks.
Office: The 75,000 sf Bruce Power Protected Area Office Complex in Ontario, built by NRB in Tiverton, was completed in 378 days. Fabricated with steel and pre-poured concrete floors, the two-storey administration building accommodates 1,200 staff. The building was placed partially over underground piping that could not be disturbed by a foundation system.
What are the advantages and constraints of modular construction?
Compared with traditional construction methods, modular offers advantages and constraints. These include:
Advantages
Shorter onsite construction timelines: Indoor construction is not impeded by weather. Concurrently, demolition, excavation and building foundations can take place onsite. This can translate into shorter timelines for delivery, greater savings, quicker occupancy and faster return on investment.
Greater cost certainty: Construction efficiency, alongside a greater ability to control costs, labour, schedules and delivery, can mean fewer budget overruns.
Better quality control: Modular components are fabricated in climate-controlled facilities which protects materials from exposure to damaging weather conditions. Precision manufacturing equipment and software, combined with continual supervision of production processes, supports the delivery of consistent, quality products.
Optimised labour and safety: Fewer job activities and fewer workers are required onsite, while the use of technology and assembly-line methods in the factory streamlines processes, enhances productivity and optimises safety.
Higher standards of environmental sustainability: Prefabrication – with its commitment to precision – can produce less waste and emit fewer greenhouse gas emissions. Modular components cut down the time and intensity of onsite construction, which in turn reduces waste materials, emissions, noise pollution and construction traffic and road closures.
Increasing customisation: Advancements in construction design software and digital tools support customisation, with building designs, features and options increasingly comparable to site‐built construction.
Benefits for end-users: For buyers, tenants and other end users, modular prefabrication offers more affordable buildings, high-quality materials and components, faster construction and more reliable timelines.
Constraints
Capacity limitations: Most markets still have modest modular manufacturing capacity among a relatively small number of modular manufacturers. While most plants can build modules for any type of building, retooling and adapting worker skills for different types of products can be costly. Since modular construction projects tend to involve only one or a few suppliers, this increases execution risk.
Upfront costs: For manufacturers, purchasing and establishing the facilities and for modular construction represents a large initial upfront investment. This can restrict the financial viability of smaller projects. Modular construction also requires more design and engineering to be completed upfront.
Skills gaps: Successful modular projects depend on skilled architects, engineers and contractors, but some markets still have limited numbers of experienced design and construction teams.
Financing and cash flow: Many lenders are unfamiliar with modular construction projects, which can make it difficult to secure financing. A lender typically provides capital in a series of tranches on a traditional construction project, and the onsite building becomes increasingly valuable as collateral. In contrast, a modular project requires much of the total capital up front, and the lender has only an empty lot as collateral. Therefore, lenders frequently require additional security, guarantees and insurance. Developers must also grapple with a new approach to cash flow, as manufacturers typically require deposits prior to final design and again prior to manufacture.
Proximity of suppliers and transportation logistics: The geographic proximity of the manufacturing facility is mission critical to modular construction. Transporting large modules long distances can offset the cost savings achieved by labour efficiency gains. A mishap during transport could also require repairs, replacements or unexpected project delays.
Compressed timing and project planning coordination: Achieving the time and cost-saving advantages of factory‐built modules demand extensive pre‐project planning, early engineering design completion and close project management. Factory fabrication also requires the design and engineering of the units to be finalised early in the manufacturing process – and that means committing early to final design. Since onsite assembly and installation is accelerated, the timing of components and contractors must also be carefully coordinated.
How can we reap the rewards of modular construction?
Governments, investors, manufacturers, developers, builders, architects, financiers and consumers can all benefit from modular construction – and there are several ways we can work together to eliminate barriers and reap the rewards. Here are the top three:
Champion the benefits: A lack of awareness about the benefits of modular building is a handbrake on growth. Take an active role to champion this evolution in the construction industry and the potential gains ahead.
Educate lenders and insurers: Some finance and insurance providers still perceive loans and insurance policies for prefabricated projects to be riskier because they are developed offsite. A clear and consistent risk framework for modular construction can help secure more affordable financing and insurance options for these projects.
Collaborate to build scale: Productive relationships are central to a reliable modular construction pipeline. Alliances can advance capacity, innovation and capital investment. Consider joining your country’s relevant association or get involved with industry-lead research initiatives.
Momentum is building. Modular construction is poised to transform construction with compressed timelines, lower costs, safer sites and higher quality builds. There are positive signs on the horizon – but the companies that reap the rewards will be those that can also manage the risks.
Authors
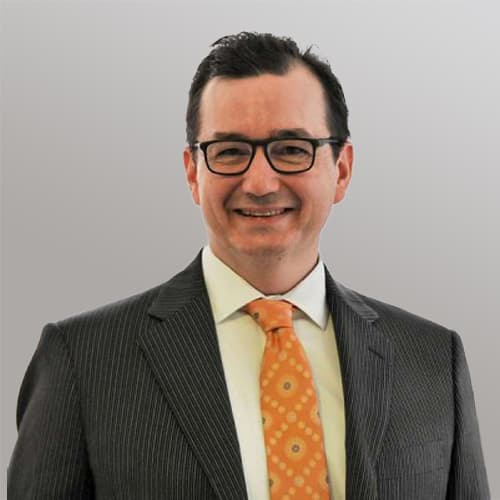
Peter Norman
Vice President and Economic Strategist
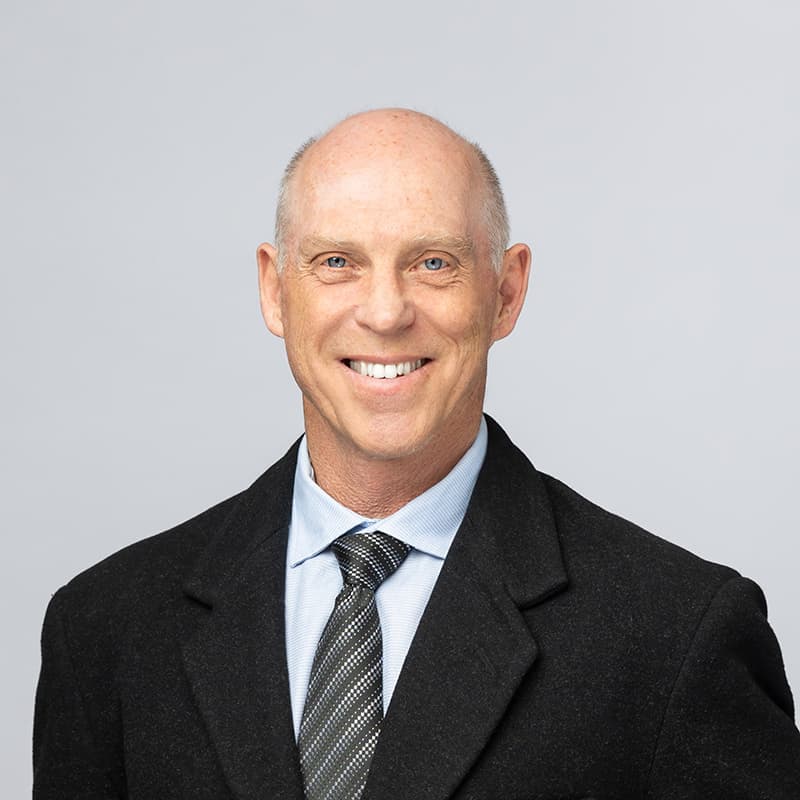
David Collins
Director, Cost & Development Advisory
Authors
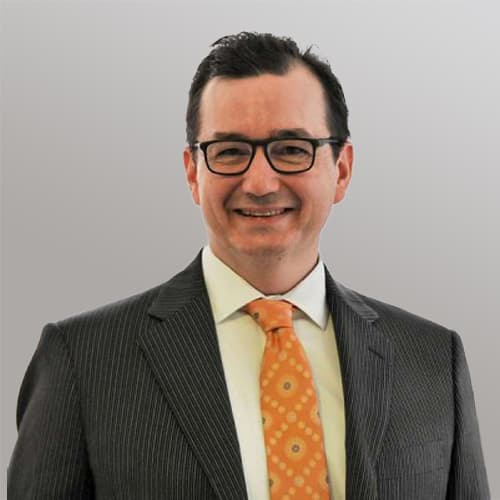
Peter Norman
Vice President and Economic Strategist
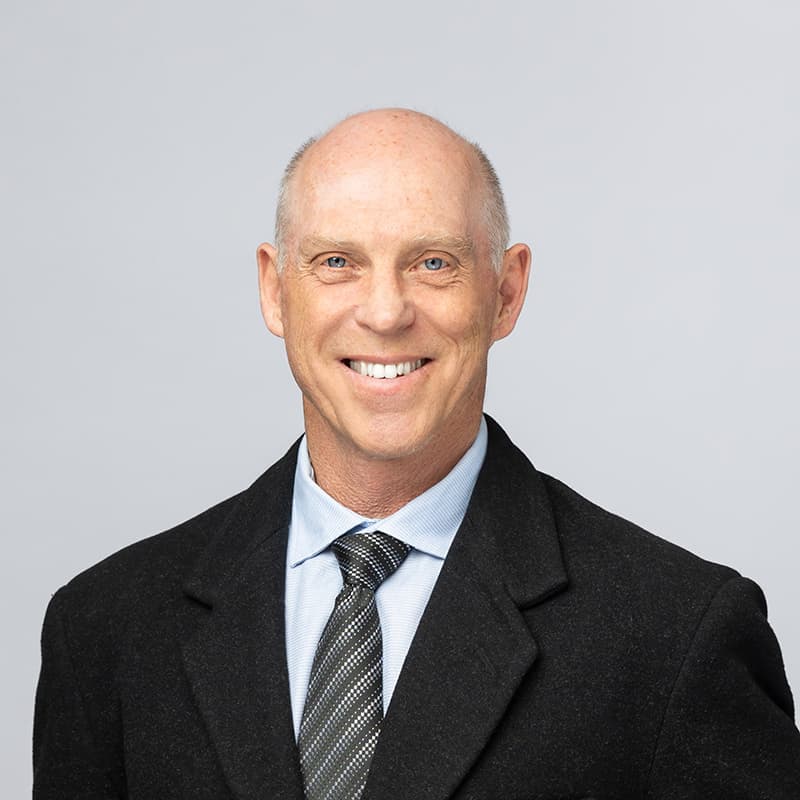
David Collins
Director, Cost & Development Advisory
Resources
Latest insights
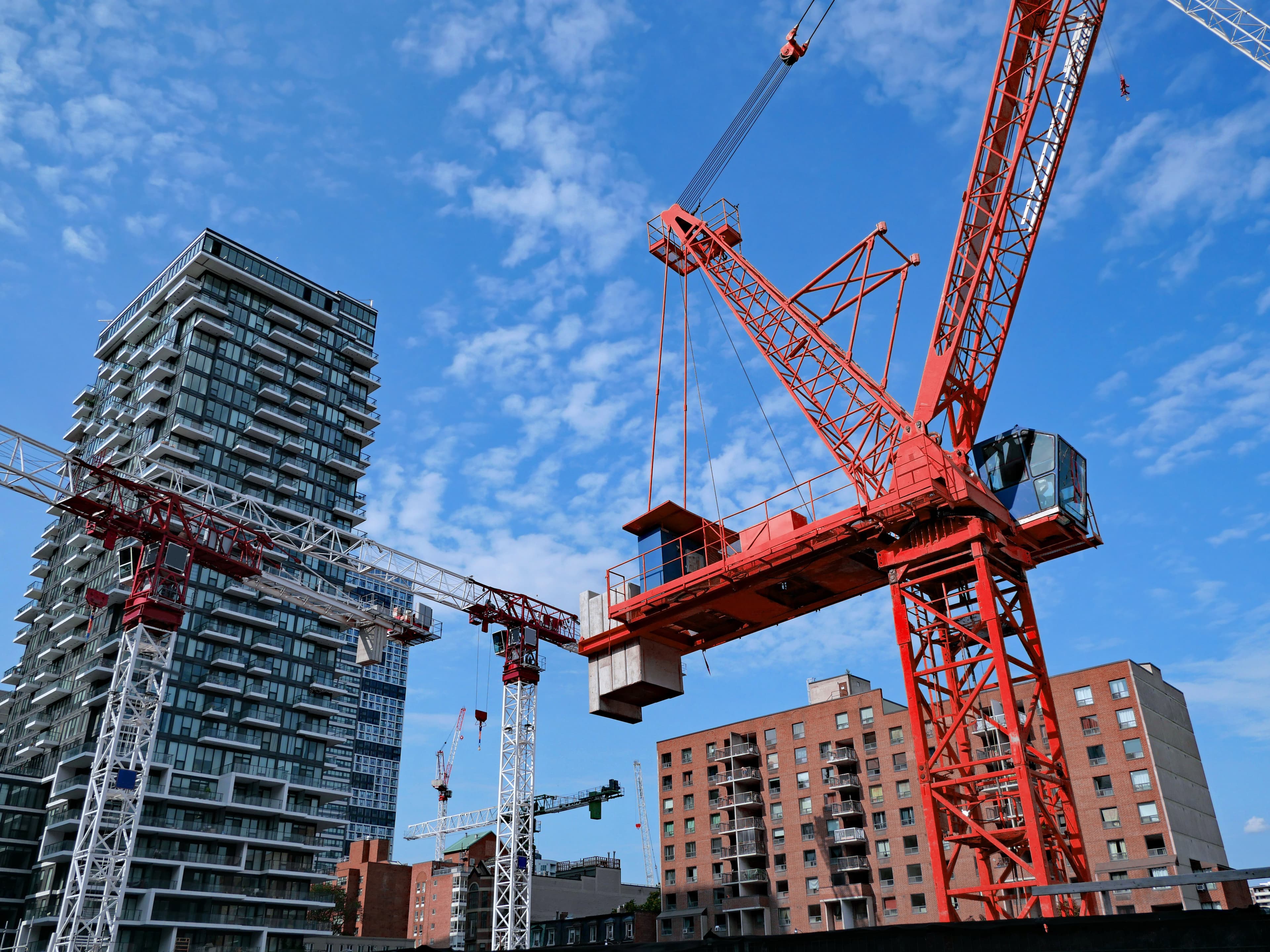
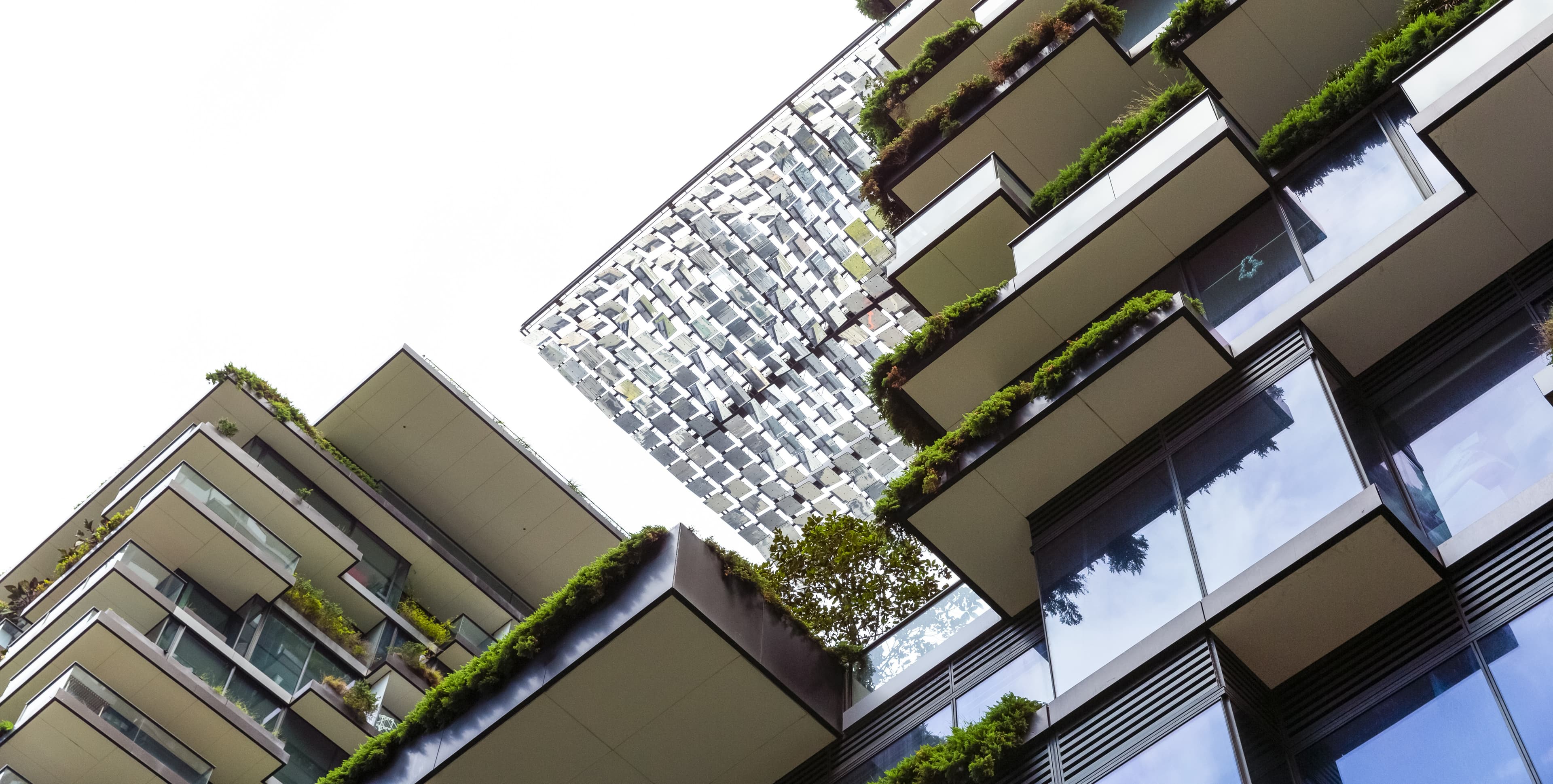
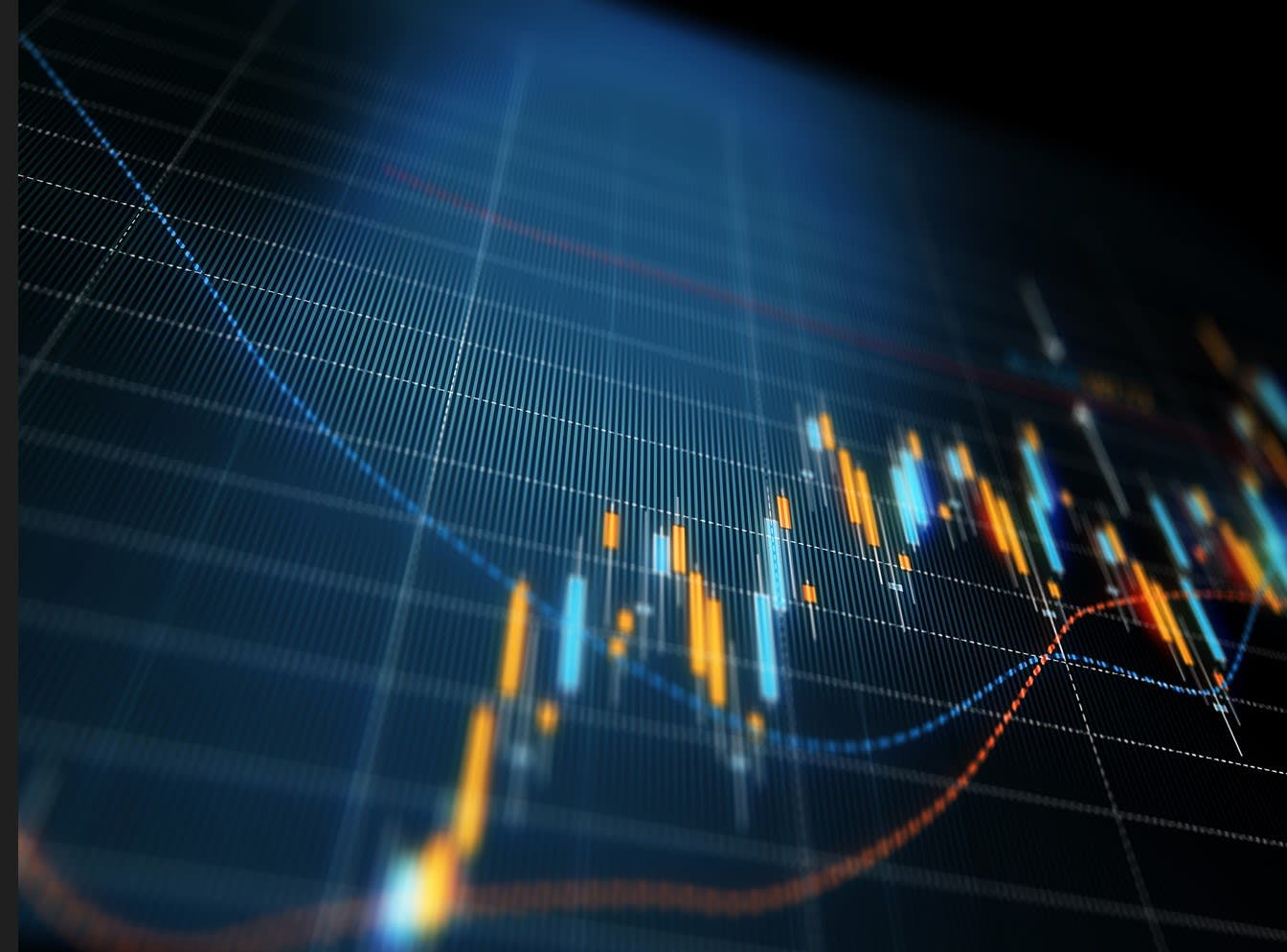
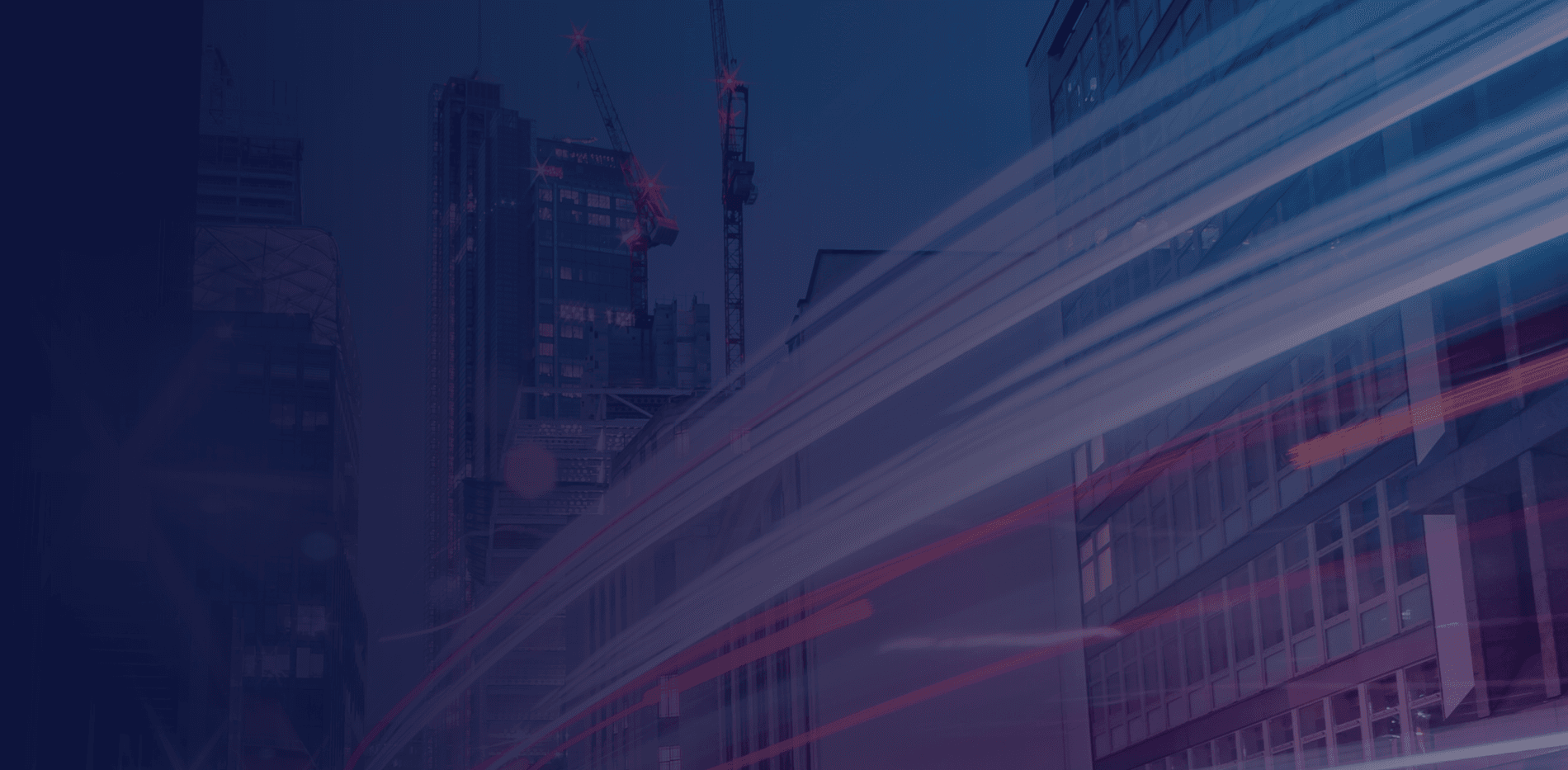
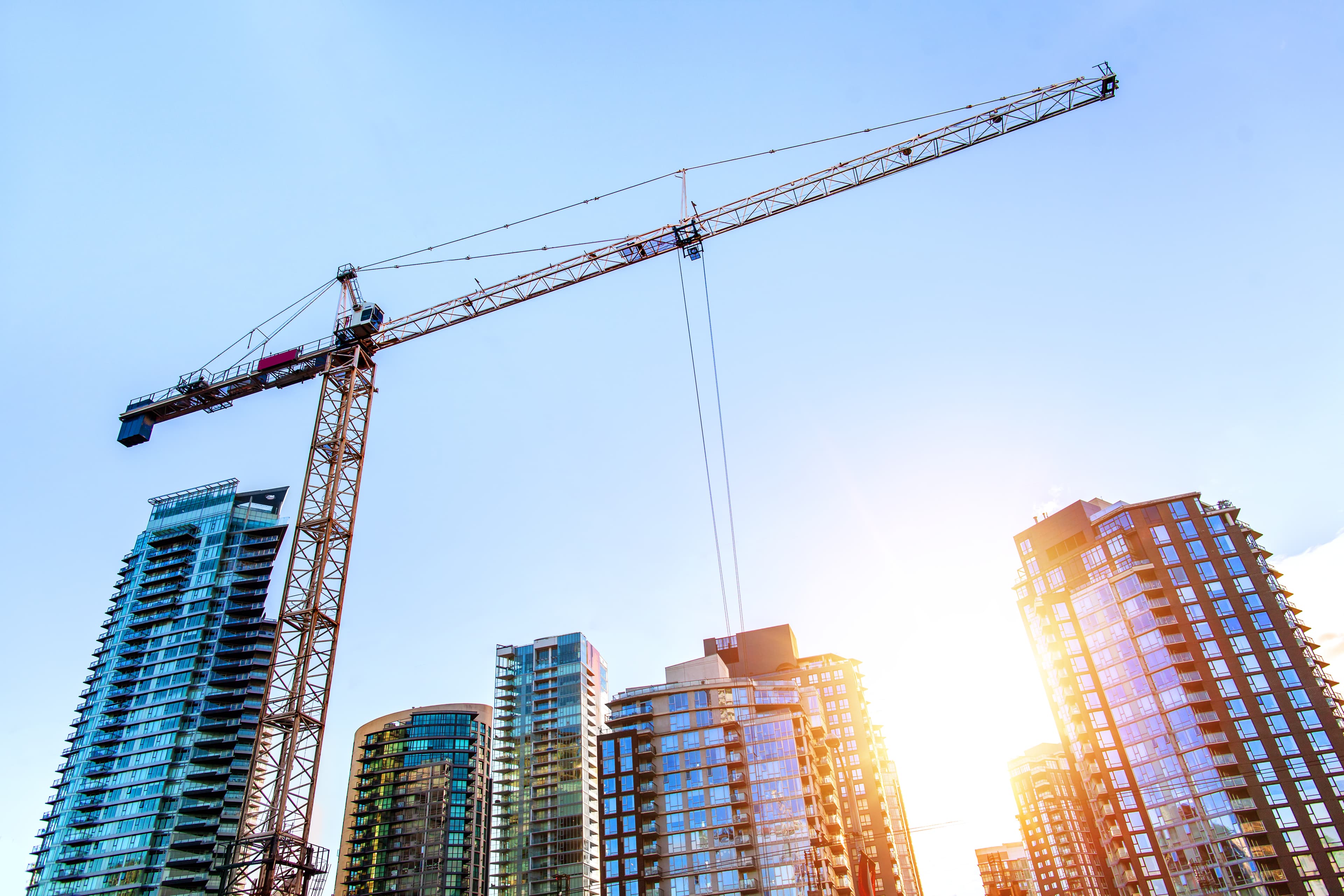
Mar 27, 2025