Cutting a new pattern - Construction’s productivity problem starts with bespoke buildings
As housing costs in Australia spiral and productivity growth stagnates, bespoke building is a luxury we can no longer afford.
Key highlights
Australia’s construction industry has an intractable productivity problem that has played out for 30 years
Wages are rising rapidly and construction costs continue to climb without corresponding uplifts in productivity; we are doing less with more
As housing costs spiral and productivity growth stagnates, bespoke building is a luxury we can no longer afford; for some projects, the only solution is standardization
Why couture construction comes at a cost
Australian construction is like haute couture fashion. Everything is made to measure, and buyers rarely want buildings that are ‘off the rack’. But we can no longer afford to pay the designer prices.
Sluggish productivity is a nationwide problem and the average Australian has $25,000 less a year in their pocket today, in real terms, than they did in the 1990s.
In the construction industry – which is Australia’s biggest employer – slowing productivity means we produce fewer homes than we have in the past. The Productivity Commission says construction labour productivity fell by 1.8% in 2023, as our population grew by 651,000 people.
Oxford Economics Australia has estimated that raising construction productivity to the economy-wide average could unlock an extra $56 billion in construction capacity every year. This would be enough to deliver 1,000 additional schools, 10,000 kilometres of road or 25,000 extra hospital beds.
The opportunity is obvious. But turning around a three-decade productivity slump requires new mindsets and new methods of construction.
Figure 1 - Australian productivity growth, 2001-02 to 2021-22
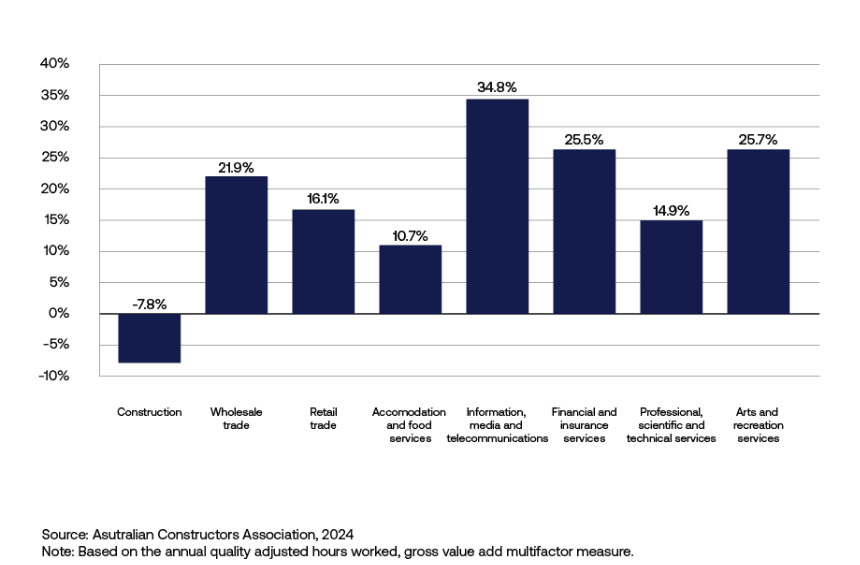
Applying the Model T mindset to modular homes
We know we have a problem. What can we do about it?
Elevating productivity requires a suite of solutions, rather than one silver bullet. These solutions are well documented, and include everything from digital technology to skills development, supply chain optimisation to red tape reduction. And yet, despite the endless reams of research, productivity uplift remains elusive.
There is no one quick fix, but the Australian Constructors Association nails it in its Nailing Construction Productivity report: “There is simply too much waste and duplication in current processes.”
Each time we start a new project – whether it’s a building or a bridge, linear or vertical infrastructure – we begin with a bespoke design.
Customisation brings complexity and cost. Bespoke demands extra time and attention to detail, limits economies of scale, and carries more risk and uncertainty.
Henry Ford famously told customers they could have their Model T painted any colour they chose “so long as it is black”. Fifteen million Model Ts were sold, thanks to repetition, standardisation, and uniform parts that reduced complexity and cost of production. Ford’s method reduced the time it took to assemble a car from 12 hours to around 90 minutes.
We are at a point in Australia’s history – where we need 200,000 new houses a year just to keep up with demand – that we need to follow Henry Ford’s example and embrace repetition, standardisation, and uniformity.
From custom to consistent and cost-effective
Standardisation challenges the classic project manager’s trade-off between time, cost, and quality.
Take Hickory's La Trobe Tower, which at 33 levels is Australia’s tallest prefabricated building. The 206-apartment building was delivered around 30% faster than conventional construction using integrated structural prefabrication, Hickory’s proprietary façade system, and bathroom pods.
La Trobe Tower demonstrates why faster construction equals cheaper construction. Constructing major structural elements offsite added other layers of value too: safer, quieter sites; less waste and fewer carbon emissions; and higher quality outcomes thanks to methods and materials that were well-tested and refined over time.
We also have training pathways in place that can help people upskill in standard building practices. Multiplex’s Centre for Excellence in Sydney is an industry-first training facility that provides physical representations of the most common risks to quality using prototypes to demonstrate best practice. Let’s replicate what already exists to standardise at scale.
In March, Australia’s Building Ministers agreed to work together to stimulate growth of prefabricated and modular construction. The Australian Building Codes Board is now working with industry bodies to reduce barriers and cut red tape. This is important work.
But one of the biggest barriers to standardised, modularised building is the Australian mindset. Critics argue that standardisation leads to monotony and lack of character. But tell that to residents of Amsterdam’s canal houses, New York’s brownstone apartments or Parisian Haussman buildings. Talk to the occupants of Sydney’s coveted terrace houses and see if they hate standardisation. Uniformity in size or building materials can be offset by distinctive façades and clever design that adds kerb appeal.
Ultimately, we are faced with some hard decisions. Choice adds to costs. To raise productivity, we must standardise. Our bespoke way of building is an aspiration we can no longer afford.
Want to be notified of our new and relevant CRE content, articles and events?
Author
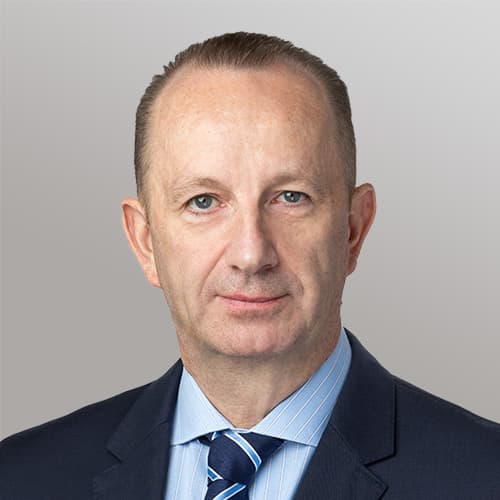
Niall McSweeney
Head of Development Advisory, Asia-Pacific
Author
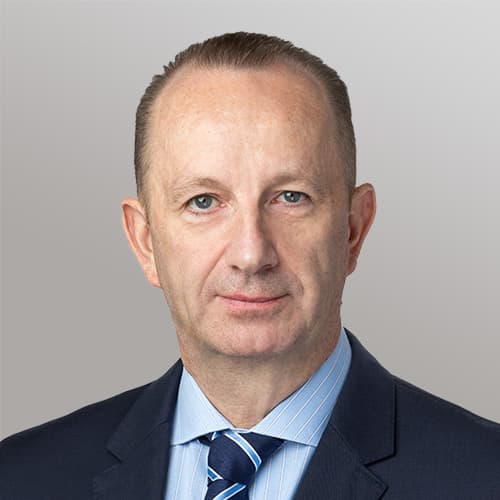
Niall McSweeney
Head of Development Advisory, Asia-Pacific
Resources
Latest insights
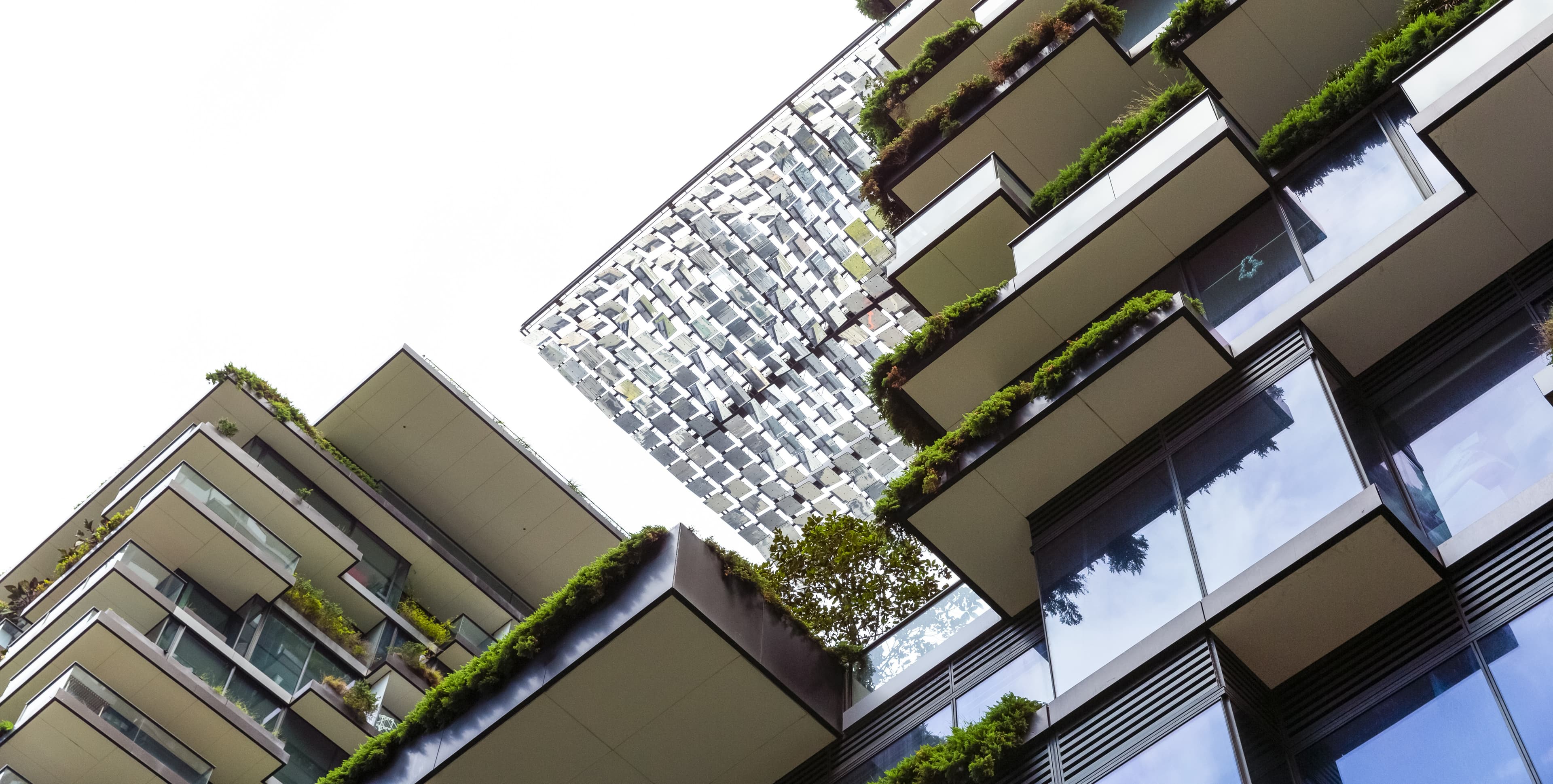
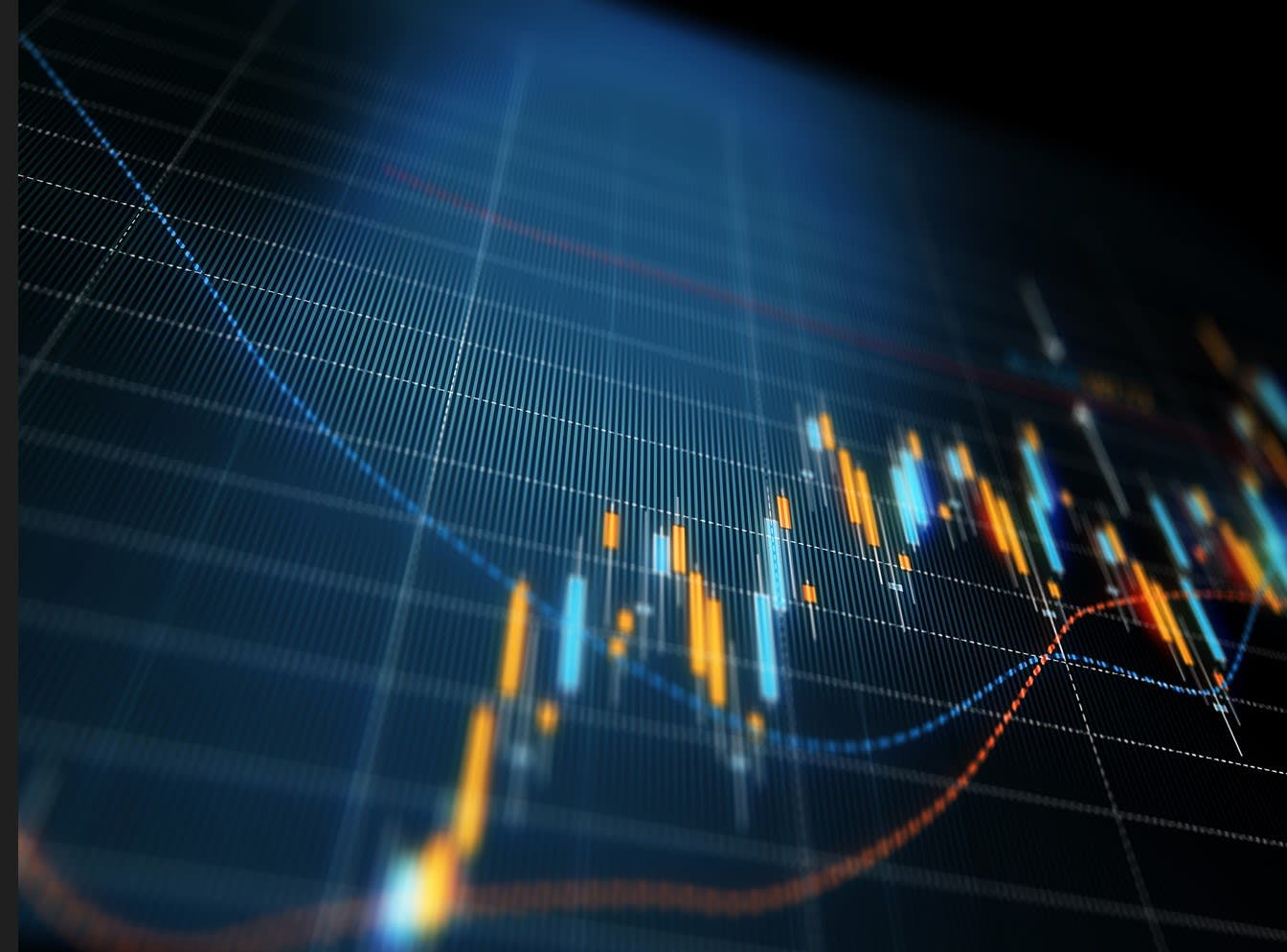
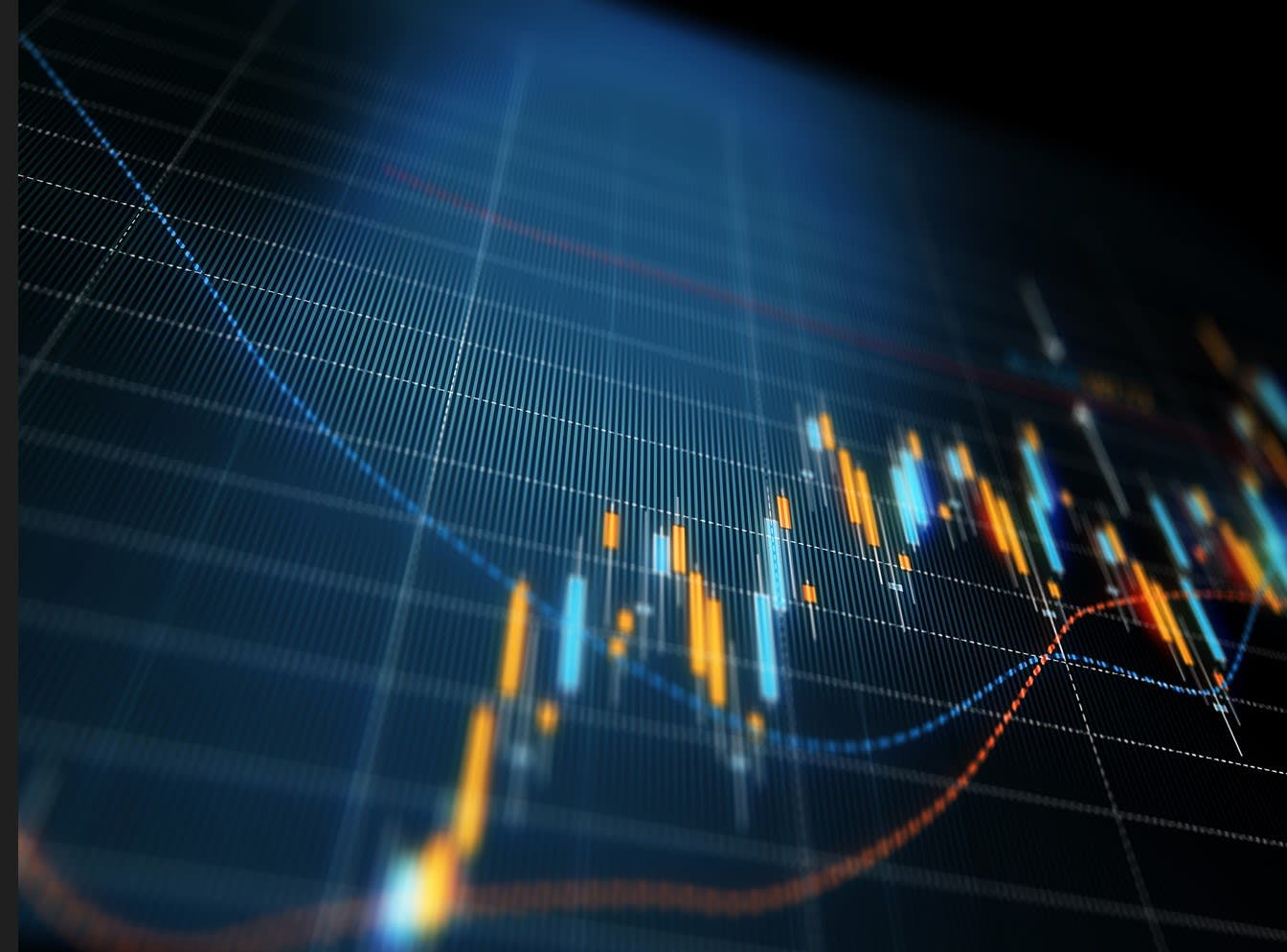
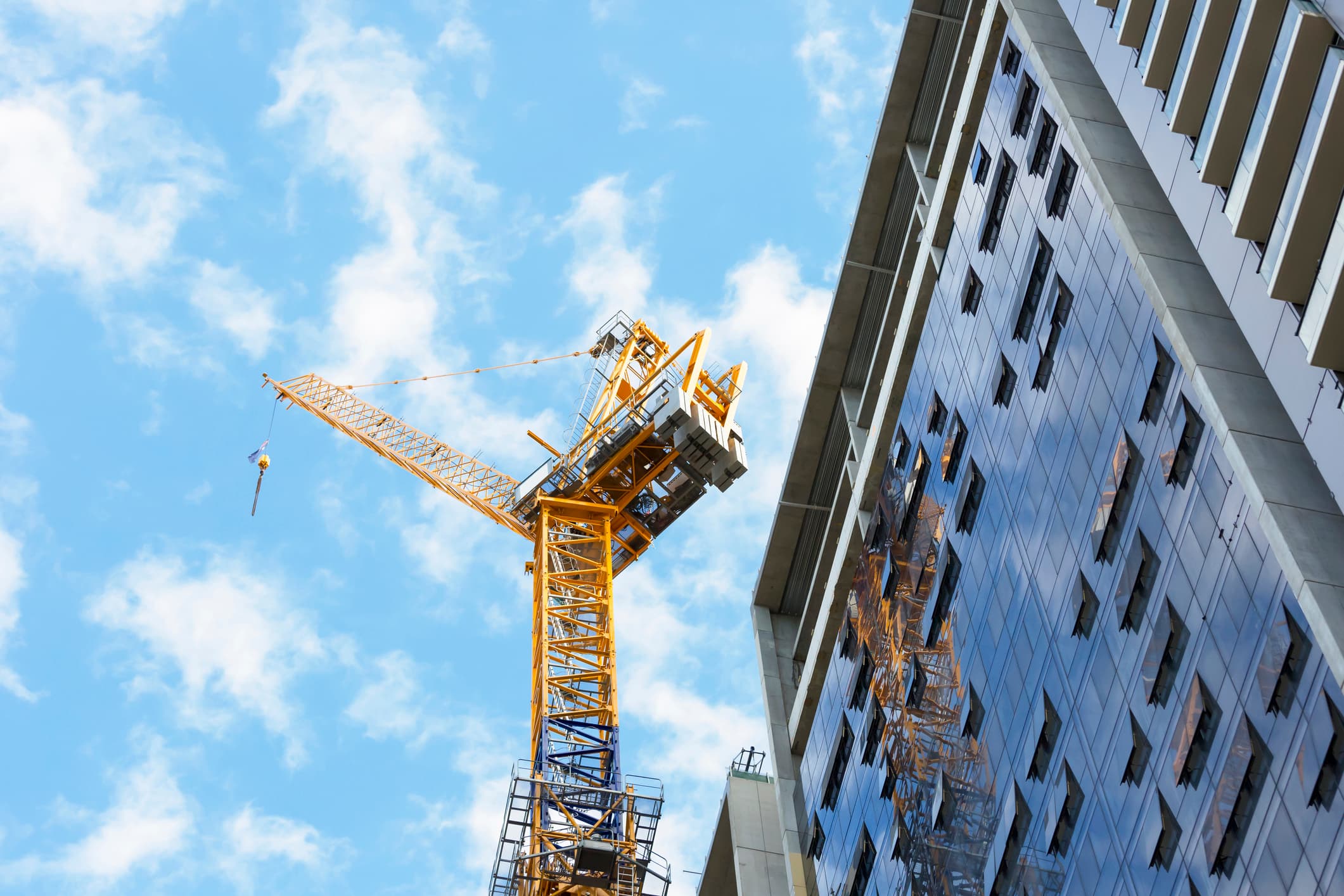
Jan 9, 2025
Building the future - Key trends shaping Australia’s construction industry in 2025
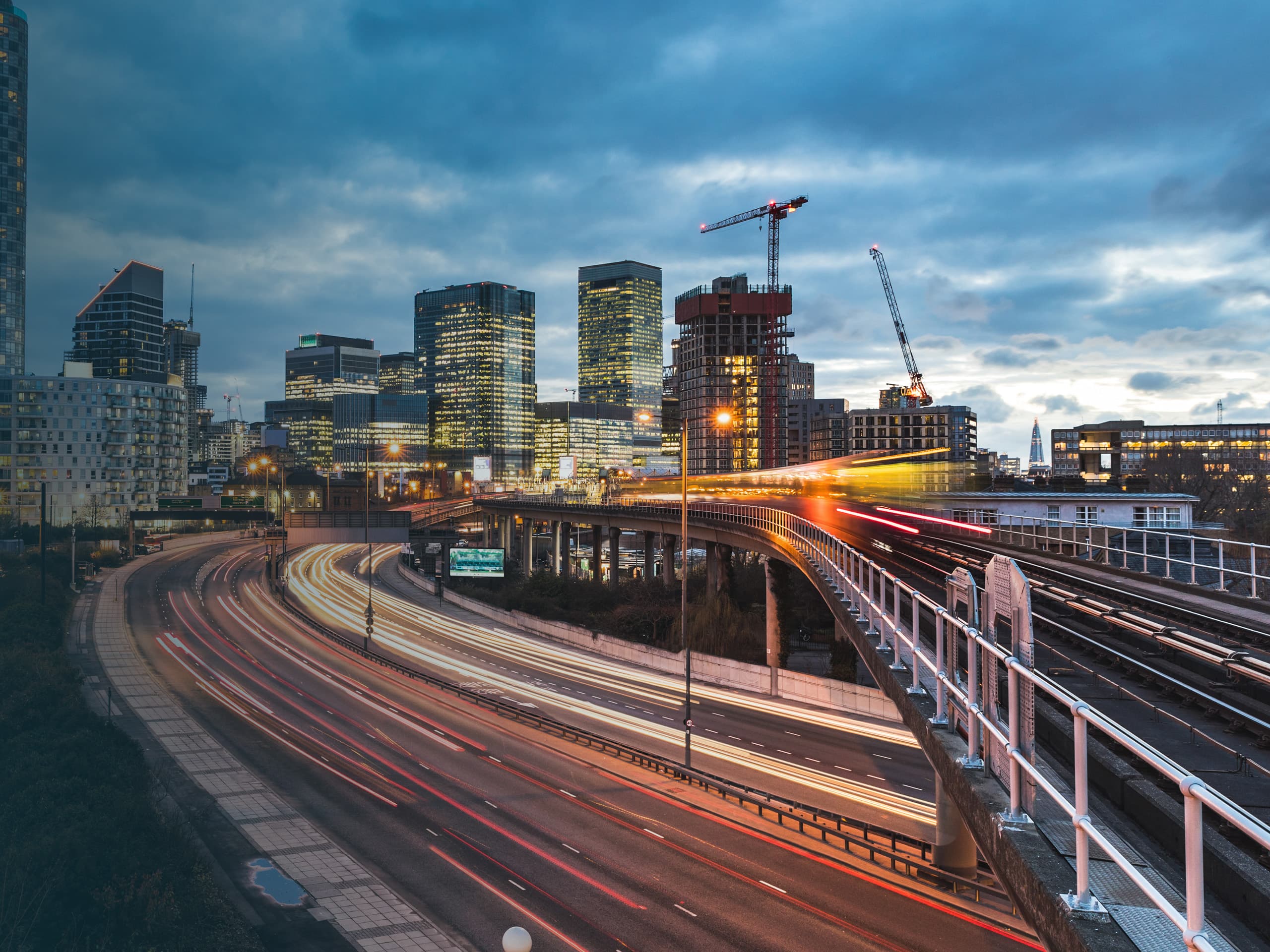