Key highlights
In a dynamic and evolving market that faces regular environmental, economic, and political disruption, identifying and addressing cost escalation challenges proactively is crucial to the success of any development project
Sector-specific nuances must be taken into consideration when managing cost escalation, as the mix of trades vary in different asset classes
Construction product rates are normally made up of three components: supply, delivery, and installation; however, different trades exhibit diverse cost structures
For any given trade, each cost component can exhibit unique escalation patterns
A reduction in product or supply costs may not necessarily result in a lower overall escalation rate, especially if it is offset by a rise in labour costs
Calculating escalation estimates by applying ‘first principle thinking’ enhances their accuracy across different project sectors and types
Beyond the generic 3-5% annual escalation
One of the most important aspects of cost planning is the management of cost escalation, especially when navigating high-value projects that extend over long durations. The post-pandemic landscape has been earmarked by inflated costs and economic volatility; as a result, numerous projects have experienced significant financial strain. Identifying and, more importantly, addressing these challenges in a proactive manner is crucial to the success of any development project – now more than ever.
Perhaps the most common approach applied to the estimation of escalation in the construction sector is the assumption of a general figure (usually between 3-5% per annum) which is grounded in the broader context of general inflation rates. This approach, while widely used, simplifies the complex dynamics of market fluctuations and specific cost drivers relevant to construction projects, and fails to account for the significant impact the price of different trades has on escalation rates.
“First principles thinking” is a problem-solving technique that breaks down a complex problem into its most basic, foundational elements, until it cannot be deduced any further. By returning to first principle while estimating cost escalation, we can dissect the key components that shape escalation rates, providing a deeper comprehension of this seemingly arbitrary percentage. We can also discern why specific trades are more critical to certain sectors than others; after all, fluctuations in a particular trade do not uniformly affect all sectors.
Sector-specific dependencies on various trades
Figure 1 - Trade group cost breakdown for different sectors (Illustrative data)
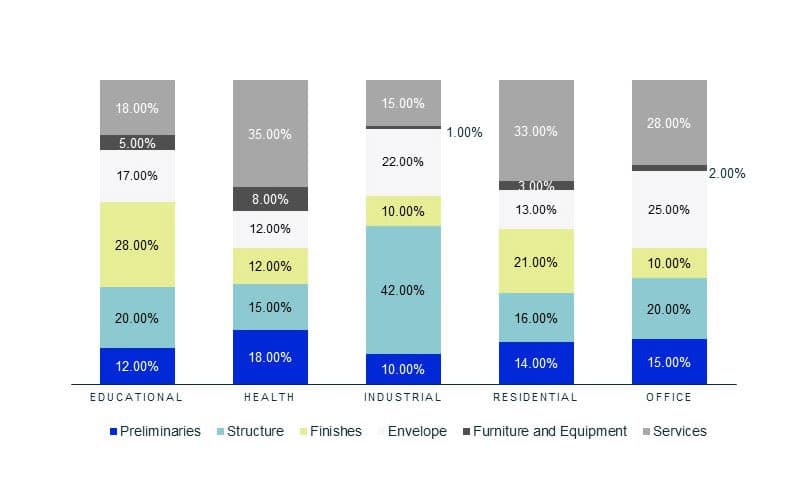
Buildings, whether they be schools or warehouses, are comprised of countless components, and no two structures are exactly alike. The cost distribution in a warehouse, for example, is heavily skewed towards structural components such as concrete and steel, whereas a hospital invests more in service trades like electrical systems and mechanical components. Consequently, a surge in prices of structural materials like steel or concrete significantly impacts industrial projects. In contrast, a rise in copper prices – crucial for mechanical piping and electrical cabling – affects a hospital project more than it would an industrial warehouse. Understandably, these sector-specific nuances must be taken into consideration when managing cost escalation.
Understanding the makeup of rates and varieties of escalation
Construction product rates are normally made up of three components: supply, delivery, and installation. However, different trades exhibit different cost structures. For instance, painting is normally labour-intensive with minimal supply costs, while the ready-mixed concrete trade has a higher proportion of supply costs. Trades like carpentry or brickwork, on the other hand, may have a more balanced distribution between supply and installation costs.
Escalation rates also vary significantly among supply, installation, and delivery costs, as each component is influenced by distinct factors. Supply costs are primarily driven by fluctuations in raw material prices, which are subject to international market dynamics and manufacturing expenses. Conversely, installation costs are more directly impacted by domestic factors, such as the cost of living and inflation rates. Delivery costs, however, are closely tied to fuel prices, reflecting changes in energy markets. For any given trade, each cost component can exhibit unique escalation patterns.
As such, it's important to note that a reduction in product or supply costs may not necessarily result in a lower overall escalation rate, especially if it is offset by a rise in labour costs. This intricate relationship underscores the need for a nuanced understanding of how different factors interplay in influencing the total cost escalation of a project.
Piecing together the cost escalation puzzle
The following table illustrates the variables impacting the sector trade cost split, component of a rate, and different escalation rate for different component of the rate. From there, the escalation rate can be calculated for different trade and different sector.
Figure 2 - Correlation Between Sector Cost Breakdown and Trade Escalation in Escalation Rate Calculations (Illustrative data)
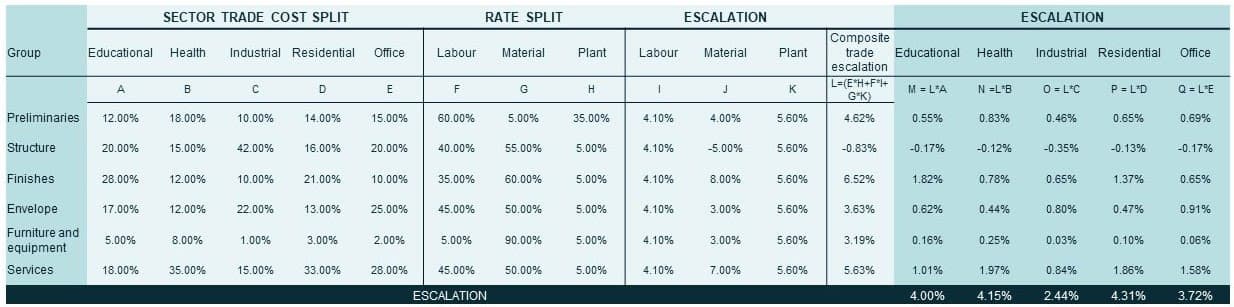
By dissecting the unique factors that drive cost changes and their varied impacts across sectors, we can derive valuable insights that unlock more accurate forecasts and feasibility studies. With enhanced predictability, development projects can avoid budget obstacles that might otherwise derail progress and profitability in the ever-evolving construction landscape.
Disclaimer
This publication has been prepared for general guidance on matters of interest only and does not constitute professional advice or services of Altus Group, its affiliates and its related entities (collectively “Altus Group”). You should not act upon the information contained in this publication without obtaining specific professional advice. No representation or warranty (express or implied) is given as to the accuracy, completeness or reliability of the information contained in this publication, or the suitability of the information for a particular purpose. To the extent permitted by law, Altus Group does not accept or assume any liability, responsibility or duty of care for any consequences of you or anyone else acting, or refraining to act, in reliance on the information contained in this publication or for any decision based on it. The distribution of this publication to you does not create, extend or revive a client relationship between Altus Group and you or any other person or entity. This publication, or any part thereof, may not be reproduced or distributed in any form for any purpose without the express written consent of Altus Group.
Want to be notified of our new and relevant CRE content, articles and events?
Authors
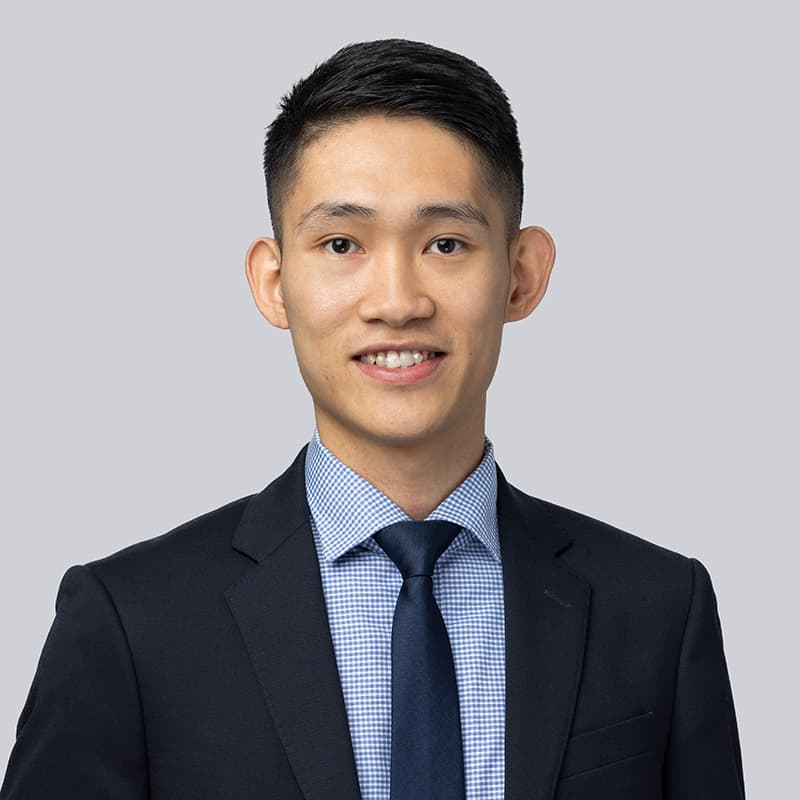
Cody Bui
Quantity Surveyor
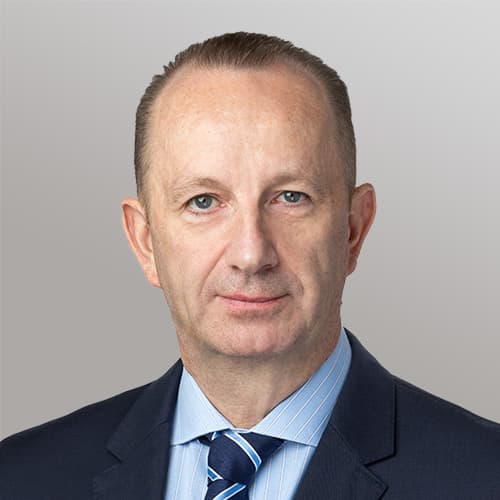
Niall McSweeney
Head of Development Advisory, Asia-Pacific
Authors
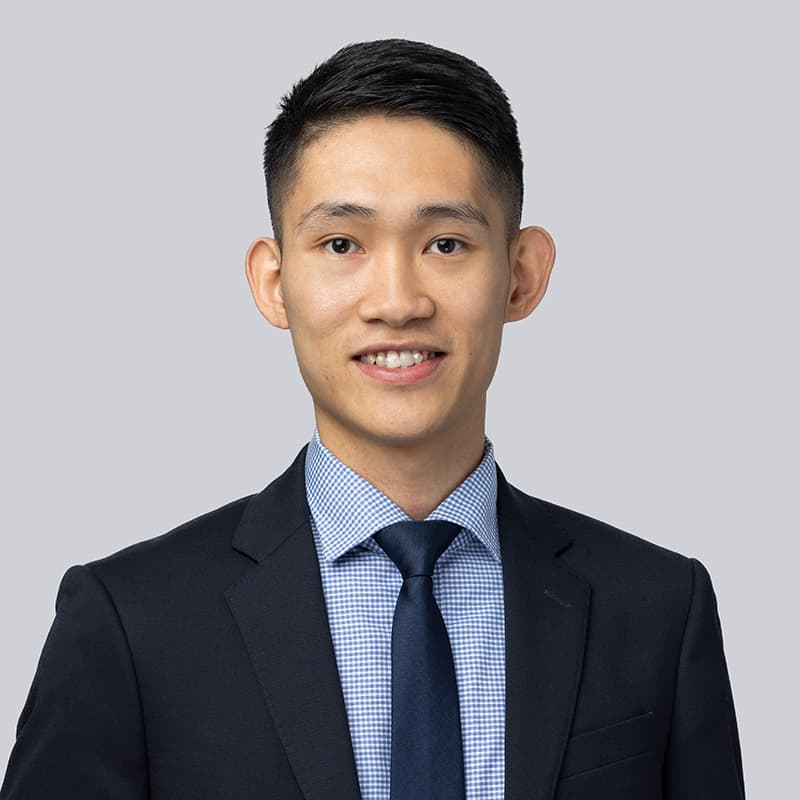
Cody Bui
Quantity Surveyor
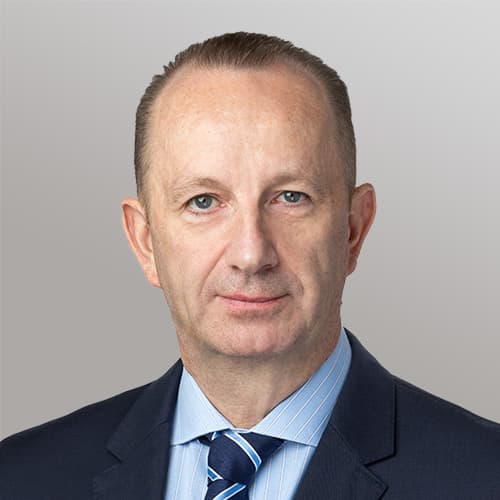
Niall McSweeney
Head of Development Advisory, Asia-Pacific
Resources
Latest insights
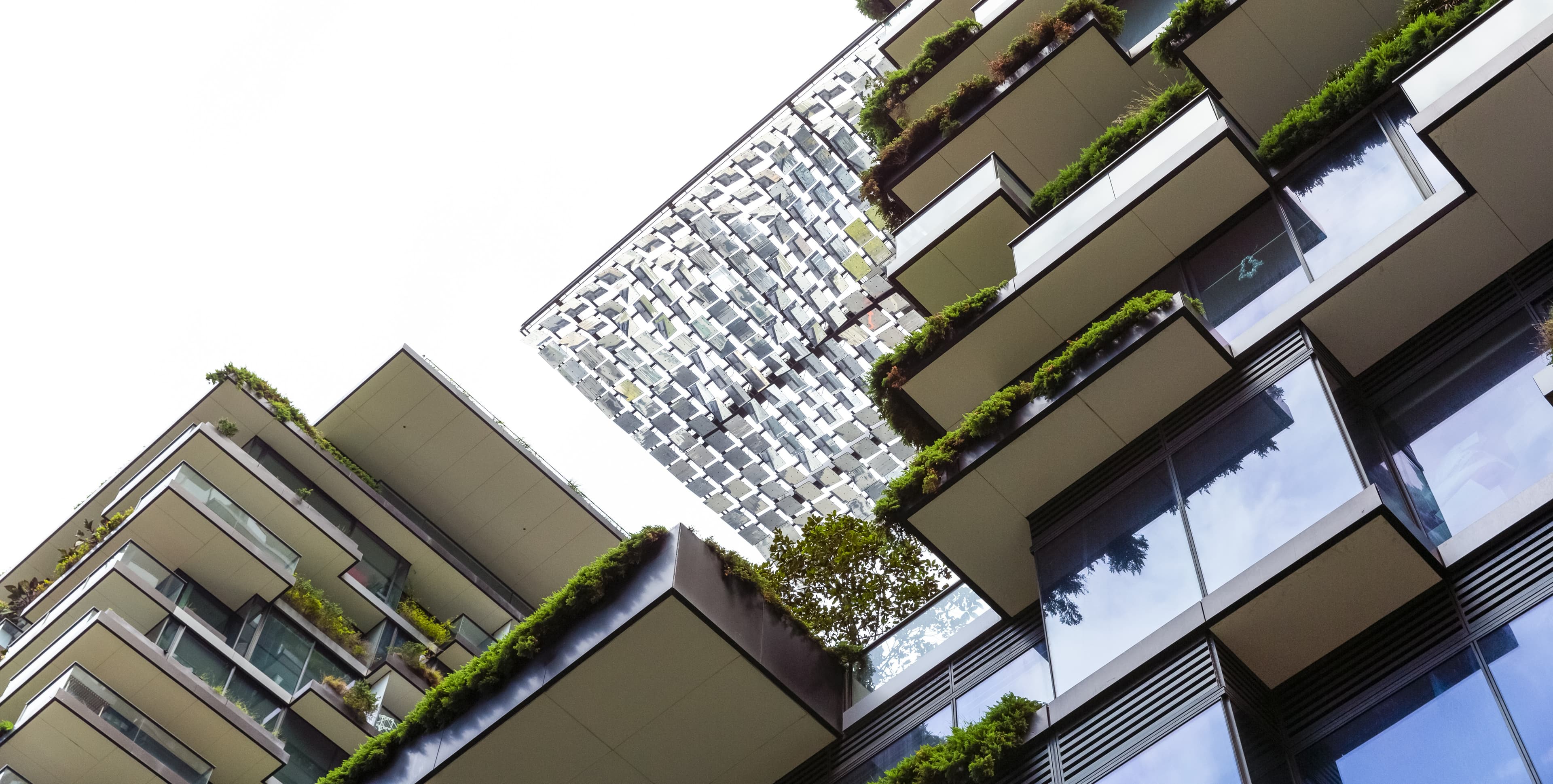
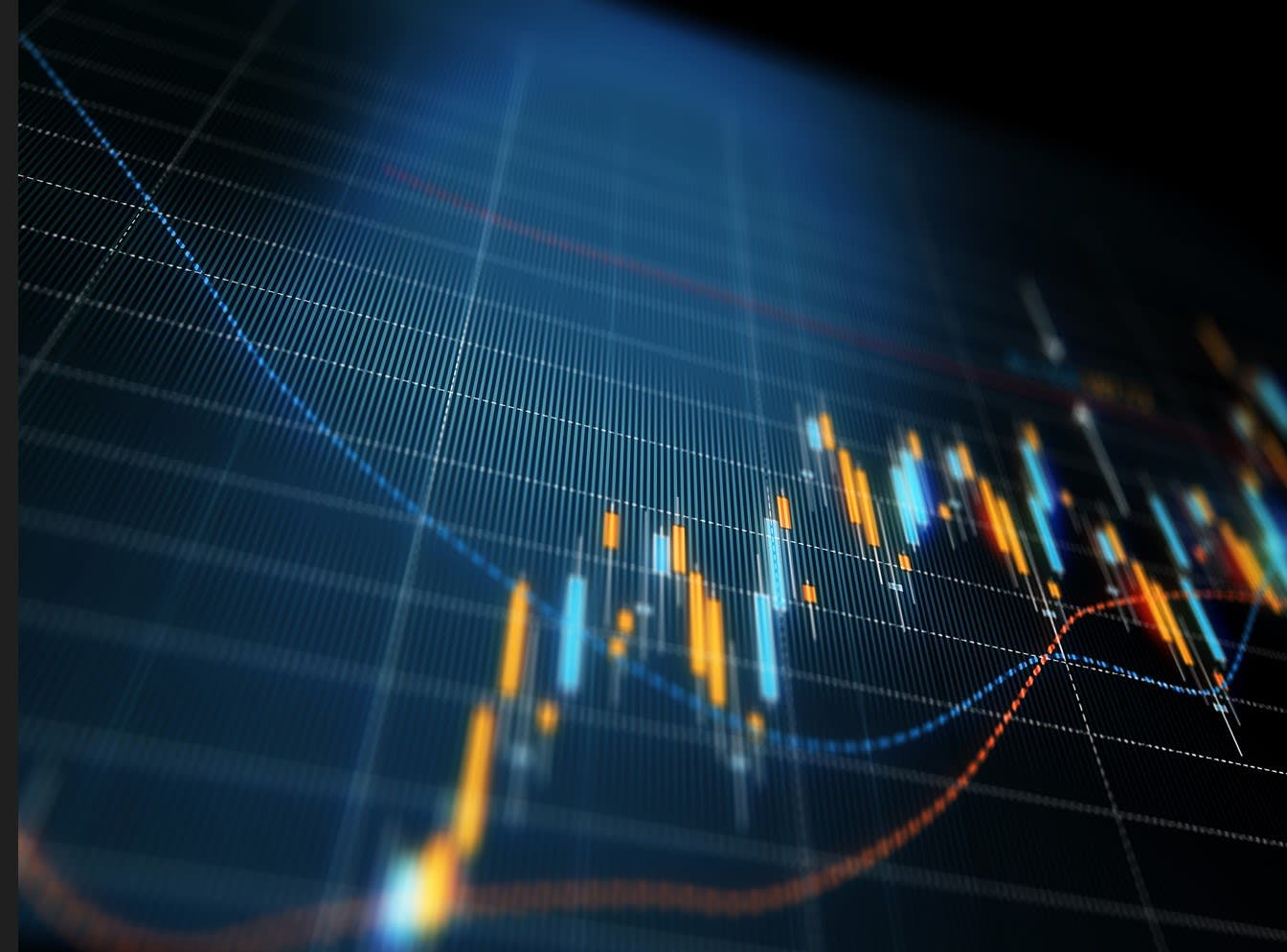
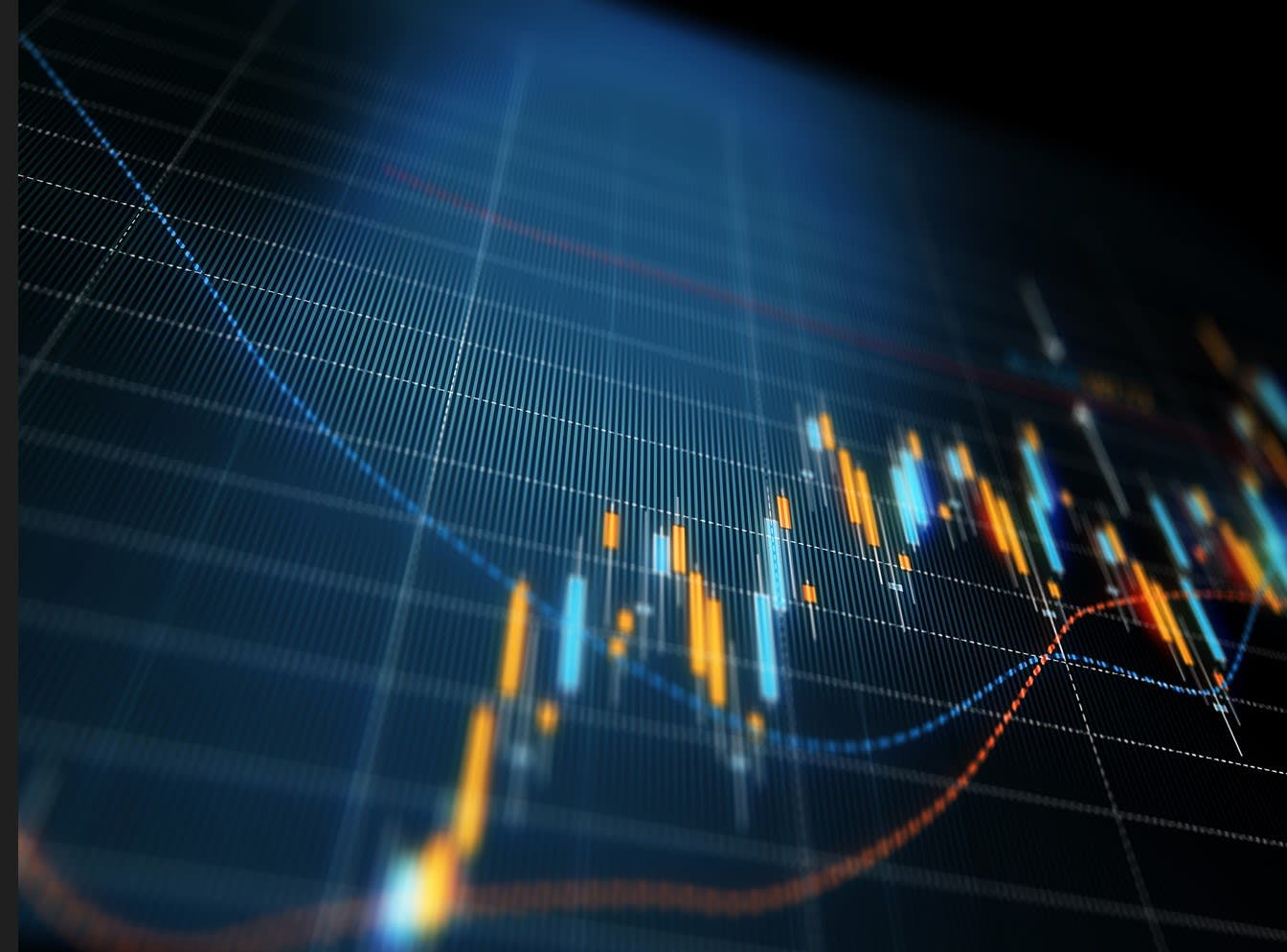
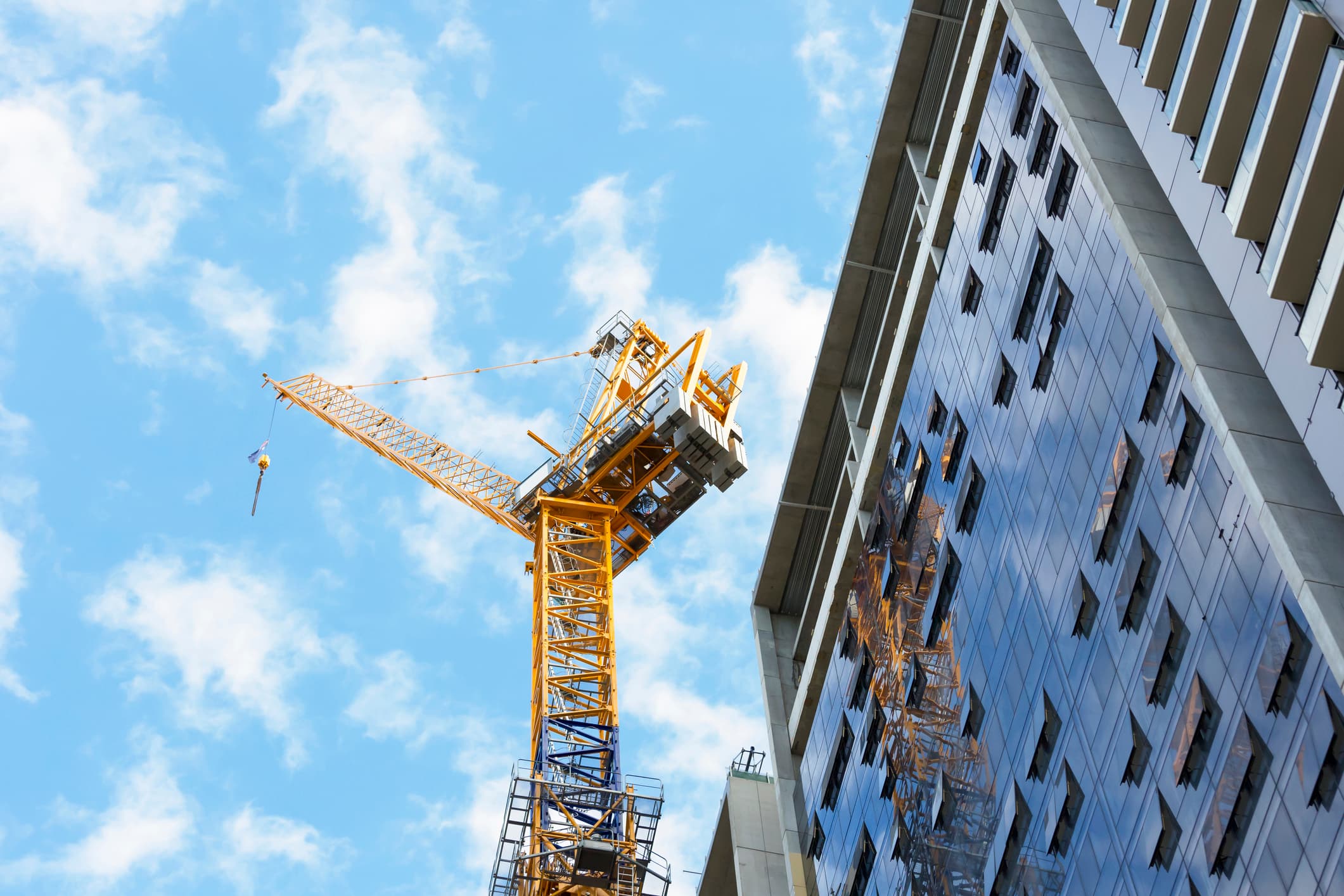
Jan 9, 2025
Building the future - Key trends shaping Australia’s construction industry in 2025
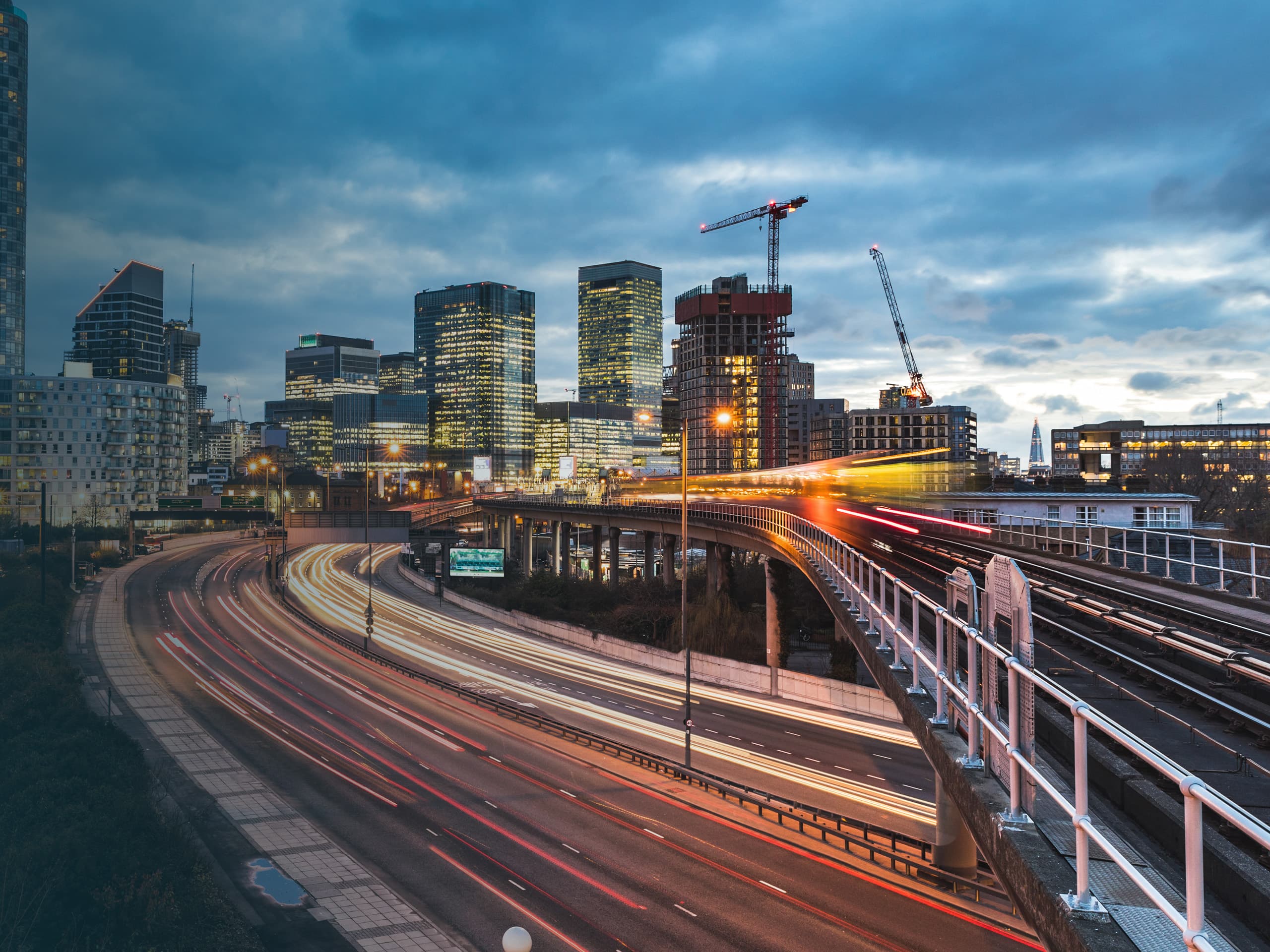